freeamfva's blog
ABOUT BIGO LIVE GIFT CARD
Bigo Live Gift Card code is known as the worldwide live video social platform where customers can live stream their thoughts, daily life moments, communicate live with relatives, friends, make videos, calls and watch great videos.To get more news about topup bigo live, you can visit topuplive.com official website.
SAUDI ARABIA BIGO LIVE GIFT CARD – KSA/SAUDI ARABIA STORE
Bigo Live Gift Card code arrives on a leading video-based social media platform worldwide. It allows potential customers to connect the world and discover tons of fun. Bigo Live platform has more than 200 million active users worldwide.
HOW TO DOWNLOAD YOUR BIGO LIVE GIFT CARD CODE?
To install, visit bigo.tv Bigo Live, you will need to select the 'Install' button indicated in the top right corner, then you can enter your Bigo Live Gift Card code and confirm. You will need to click "Direct Recharge Points" as payment option, then you can select the denomination and insert the Bigo Live Gift Card code.
INSTANT EMAIL DELIVERY OF BIGO LIVE GIFT CARDS
After purchasing the Bigo Gift Card, your gift card code will be sent to the e-mail address you entered. Your Bigo Gift Card code will be delivered instantly without waiting for you.
If you have any issues redeeming your Bigo Gift Card code, do not hesitate to contact our customer service team who will assist you in correcting the issues you are experiencing.
BE CAREFUL OF GEOGRAPHICAL LIMITATIONS
Bigo Gift Cards have regional restrictions that you should be aware of that your account region must match the region of the Bigo Gift Card you intend to purchase.
What are rotor stator pumps, and how do they work?
Rotor Stator pumps are progressive cavity pumps - a type of positive displacement pump. They can be used for pumping various viscous and abrasive fluids. To get more news about SEEPEX Pump Parts, you can visit hw-screwpump.com official website.
The fixed stator and the rotating component, the rotor, are the yin and yang of progressive cavity pumps. The rotor is the spiral steel shaft that creates conveying chambers of the inner outline of the rubber tube. Stators are metal tubes with internally molded cavities made of synthetic or natural rubber.
When the rotor is triggered, the conveying chambers move in the direction of flow. This is how the constant flow of material is achieved. The rotor takes a form which resembles a corkscrew, which, combined with the off-center rotary motion, gave its alternative name: eccentric screw pump.
2. What are rotor stator pumps used for?
Various industries use progressive cavity pumps. Putzparts is specialised in rotor stators for the construction and refractory industry to pump screed, mortar, grout, gypcrete, plaster and fireproofing cement.
Rotor stators also cater to wood processing and cellulose production, the chemical industry, the petroleum industry, domestic and industrial sewage, and low flow, high head, and agricultural water pumping.
3. What are the relevant factors when choosing the rotor stator?
Size, diameter, grain of the material, and the flow rate you want to achieve
You will want to choose your rotor stator based on its size and diameter, depending on the grain of your material and your desired flow rate. Different rotor stator pumps to suit different materials and purposes and achieve different pumping results. Different flow rates and pressure stabilities are achieved by varying designs of screw pumps.
4. Maintenance-free or clampable rotor stators?
Maintenance-free stators are more user-friendly. They can be used directly after being installed in the machine. They have unslotted steel tubes as outer casings. This means they allow for constant delivery pressure and support a hassle-free process.
Clampable stators are clamped according to material and grain size. They come in two types: stators with built-in tensioning clamps and slotted stators that are provided with an external tensioning strip.
Both transport diverse materials smoothly, continuously and with minimum pulsation. Pumps which require clamping have an integrated clamping bar or a grooved stator for the clamp, with or without an additional separate clamp. When the delivery pressure drops, the stators must be retightened.
5. How to choose the right shore for your rotor stator?
The shore is very significant: the smaller the number of the shore, the softer is the rubber. We recommend a soft rubber if you pump material with sharp aggregates, as they wear out less quickly.
6. Does Putzparts supply high-quality rotor stator pumps?
Putzparts rotor stators are made in Germany. Our high alloyed steel rotors are never hollow. We use precisely drilled, high-quality steel for long-lasting rotors.
Our stators use high-endurance rubber, which makes them long-lasting, reliable, and supportive of a solid, consistent pumping experience.
7. Can I use the pumps for different machines?
We provide Rotor Stator Pumps for various machines by Putzmeister, PFT, M-Tec, Uelzener, Turbosol, Mai, Utiform, Inotec, Imer, Brinkmann and many more. Many machines use the same rotor stator types.
For plaster, the most popular pump is the D6-3, which has a solid output of 30 litres per min at 400 rpm. If you need more, you can go with the D8-2, which has more output at 66 litres per minute than any other D-pump.
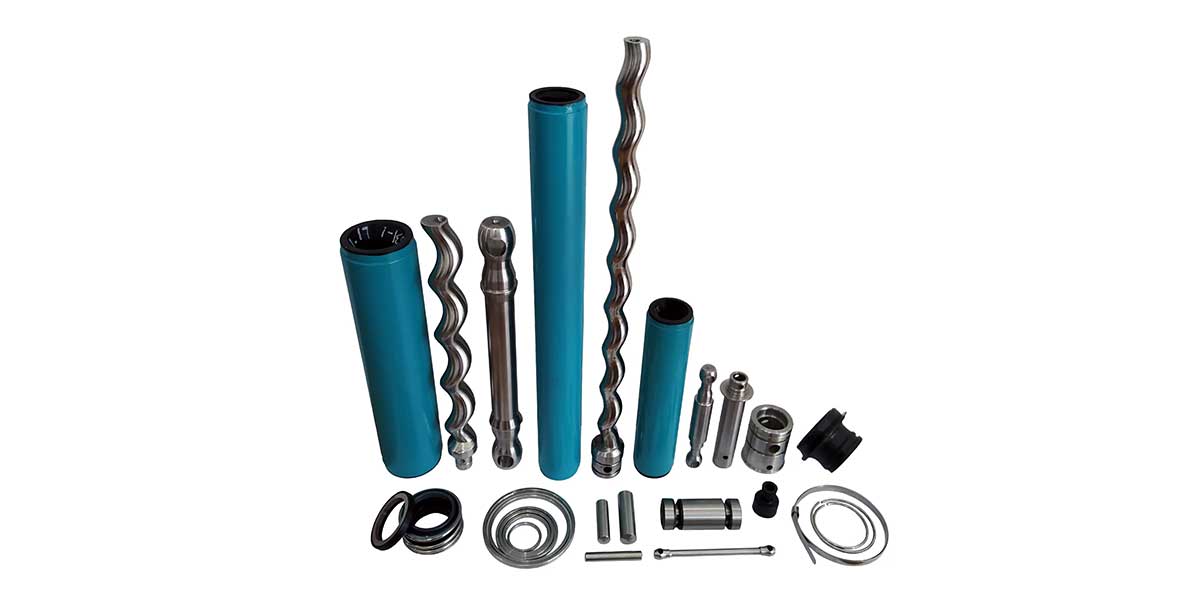
More Information on Solving Helical Rotor Pump
Pumping Abrasives with Progressive Cavity, Helical Rotor, Eccentric Screw Pumps. Often used to pump slurries, helical rotor pumps (also known as progressivity cavity pump, eccentric screw pump, mono pump) use a spiral rotor to move a chamber full of product through the pump. When moving slurries it is critical that the rotor wipes the rubber or elastomer stator firmly, else fine particles get between the rotor and stator and rip material out. This article discusses a major operating problem when the wrong size rotor was used in a stator.To get more news about SEEPEX Pump Parts, you can visit hw-screwpump.com official website.
Keywords: pumping abrasive, pumping slurry,progressive cavity pump, helical rotor pump, eccentric screw pump, mono pump
It’s been an absolute nightmare finding out what to do with a single stage progressive cavity pump that kept chopping out rotor and stator regularly for the past six months.
It was moving a 5%, 0.5 mm diameter sand slurry. No one knew what had changed. It had worked fine for 4 years during which time the rotor and stator was changed every 4 to 6 months. Then suddenly we were changing a rotor and stator every week or two.
What we found was that eight months earlier the supplier had recommended a change in rotor tolerance because of high process temperature. He suggested we try a thinner rotor to allow for expansion due to the temperature rise. We agreed to test it and in error the new item became the standard replacement part. New thinner rotors were brought to replenish stock.
The new rotor did not last long and a spare was installed. The spare was the thinner rotor. The rotor again did not last long and the spare was taken from store. It was a thin rotor. The spare was replenished but it was again with a thin rotor. These thin rotors kept being used at each repair.
This continued until production was severely affected. A thorough investigation highlighted the problem and it was corrected and previous bigger diameter rotors were put back into stock.
Have a very tight compression between the metal rotor and rubber stator so the rotor firmly wipes the stator and forces any fine abrasive along with the progressive cavity. We measured 0.8 mm difference in rotor diameter (nominally 50 mm diameter) between the thinnest and thickest rotor. The 80 C temperature rise would never have expanded the rotor to fill the gap created by using such a thin rotor within the stator.The pump supplier was concerned that with too much pressure between rotor and stator it was possible to rip the rubber out of the stator due to friction from the rotor. We have not experienced such failures in our processes, but I have no doubt that it can happen with certain products.
The larger 0.4 mm gap between rotor and stator let the pump pressure recirculate and squeeze the particulate into the space between rotor and stator.The rising pressure through the pump pushes and deforms the rubber in the stator. The sand trapped against the upstream curves of the rotor rip across the deformed rubber stator as the rotor turns and both are scored.
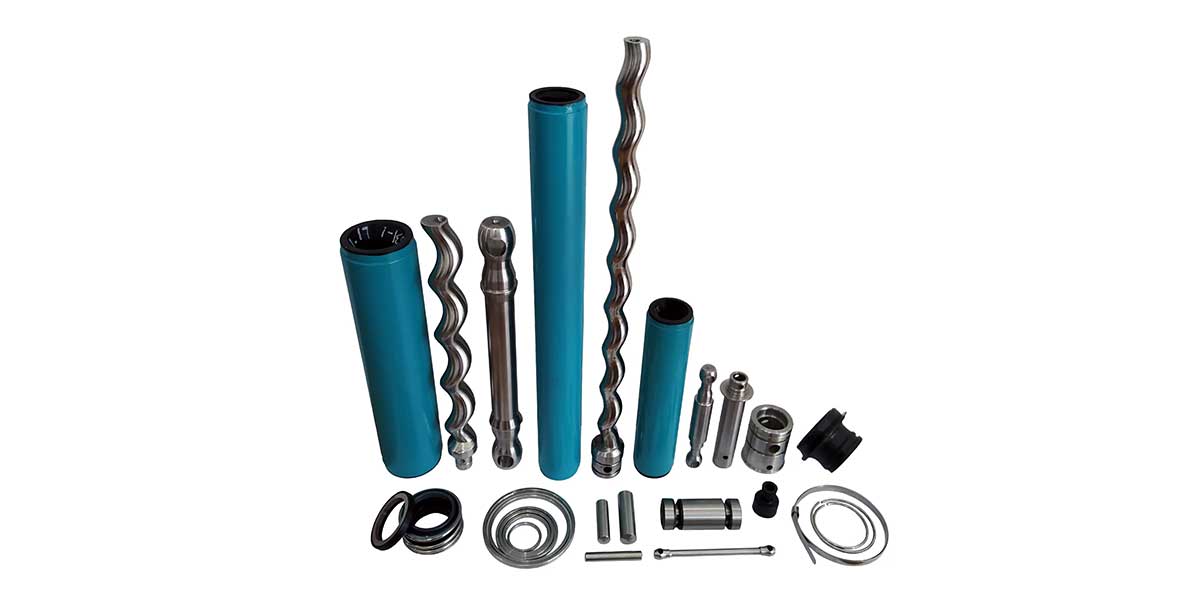
Roller Profiling for Generating the Screw of a Pump with Progressive Cavities
Progressive cavity pumps are used in industry for the circulation of high viscosity fluids, such as crude oil and petroleum products, sewage sludge, oils, salt water, and wastewater. Also known as single screw pumps, these pumps are composed of a single rotor which has the shape of a rounded screw, which moves inside a rubber stator. The stator has an double helical internal surface which, together with the helical surface of the rotor, creates a cavity that moves along the rotor. The movement effect of the cavity inside the stator is the movement of the fluid with a constant flow and high pressure. In this paper, an algorithm for profiling the rollers for generating the helical surface of the pump rotor with progressive cavities is proposed. These rollers are constituted as tools for the plastic deformation of the blank (in case the pump rotor is obtained by volumetric deformation) or for its superficial hardening.To get more news about Screw pump rotor, you can visit hw-screwpump.com official website.
Pumps with progressive cavities allow the circulation of fluids with high viscosity at a constant flow and high pressure [1,2,3]. Among the most used progressive cavity pumps are single screw pumps, consisting of an external helical rotor that rotates eccentrically inside a double internal helical stator [4,5]. The active surface of the rotor is a cylindrical helical surface of constant pitch, and the stator, whose active surface is a double helical surface, is also cylindrical and with constant pitch. The stator is usually made of rubber [6,7], and the rotor is made of steel, often superficially hardened. The exploitation activity of the pumps with progressive cavities has highlighted the fact that traditional pumps with a rubber stator, which surrounds the rotor, do not allow the existence of an interstice between them, which limits their activity until the stator wears out [8,9]. Alternatively, a new class of pumps that do not use elastomers has been developed, in which the rotor and the stator are made of metal, and are used in drilling activities in high temperature wells [10,11,12,13]. This eliminates the wear and greatly increases the lifetime of the pump for use with viscous, high density, and abrasive liquids, and with liquids containing material in suspension. To ensure proper operation, there must be a space between the rotor and the stator to ensure the leakage of the fluid. If this space is not well defined in the rotor and stator design stage, the efficiency of the pump will be seriously affected. Consequently, dimensional designs and optimizations of the rotor and stator, respectively, using analytical and dynamic simulations of the fluid flow through these pumps, have previously been explored [14,15,16,17,18].
The productive functioning of pumps with progressive cavities depends on proper design of the rotor profiles, respecting the technical conditions of their form. The cross-section form of helical pump rotors as ensembles of profiles associated with the rolling centrodes are determined based on the fundamental theorems of the enveloping surfaces (curves) and calculated based on Olivier’s first theorem, the Gohman general theorem, or the Willis theorem (normals method) [19,20].
The geometric characteristics of the rotor, namely, the helical surface with long length and rounded profile, determine that it can be processed by volumetric deformation, using tools in the form of profiled rollers with axes parallel to the axis of the processing blank. The algorithm by which the tool profile can be determined contains the following steps: defining the analytical equations in the own reference system of the piece of the generated profile; defining the absolute movements of the piece and the blank during the generating process; defining the relative movements between the piece and the tool; calculation of the trajectories of the points on the piece profile that execute a relative movement towards the tool; defining the condition which allows the determination of these points, called the enveloping condition—these points belong to the trajectory’s family and to the enveloping of that family; and association of the enveloping condition at the equations of the trajectory’s family, a connection that allows the determination of the parametric equations of the tool profile [21,22]. The tool’s profiling for generating surfaces of the rotors and the stators of the pump can start either from a physical model or from 3D models obtained by rapid prototyping. In practical activity, the determination of the rotor and the stator form can be undertaken with the help of measuring machines in high precision coordinates when the axial profiles of the generating tools in numerical form are known [23]. By comparison, these axial and graphical profiles can be determined using facilities of programming and graphical representation environments, such as the CATIA software application [
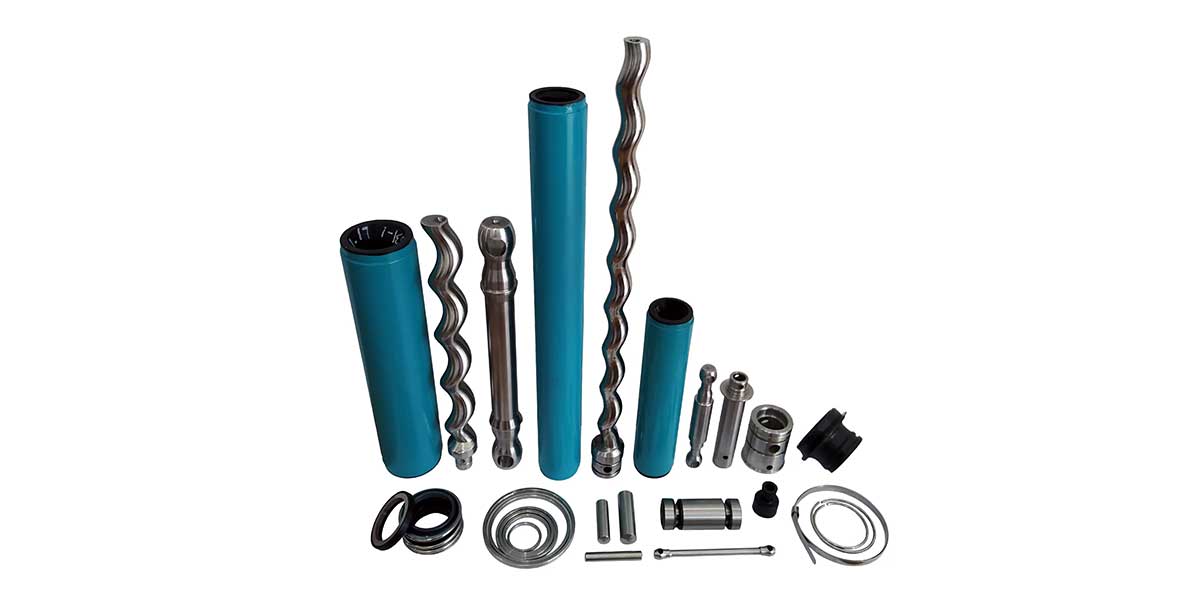
Stators for eccentric screw pumps
In the field of materials handling, progressive cavity pumps are successfully used for tasks that exceed the technical possibilities of pumps of conventional design. They have decisively expanded the range of available conveying systems and are used for conveying highly viscous, abrasive and corrosive media. The components of the progressive cavity pumps are the fixed stator and the rotating component, the rotor. Rotation and the design of both components create chambers through which the respective media are transported from the suction to the discharge side of the pump. To get more news about screw pump stator, you can visit hw-screwpump.com official website.
Stators consist of a steel jacket lined with rubber. The composition of the rubber compound in the stator depends on the requirements of the progressive cavity pumps and the medium to be pumped.
In materials handling technology, not only the abrasion behaviour but also the given physical, chemical and thermal medium properties are important factors that affect the composition of the material in the stator. The rubber mixture is therefore composed in such a way that the material wear of the stator is kept as low as possible. This increases the service life of your stators and prevents costly failures.
In paper mills, pulp, groundwood, glue and paint must be conveyed by means of stators. These are media of crumbly consistency, medium to high viscosity and chemical aggressiveness. The stators from Artemis guarantee a long service life of the progressive cavity pumps.In the food industry, eccentric screw pumps are replacing old, manual processes in the harvesting of grapes, fruit and olives. They are also used in the dairy industry or in the confectionery industry to convey highly pasty masses such as chocolate, marzipan and dough. Our materials and stators used in the food industry meet the strict requirements and quality standards of the food law thanks to our quality controls.
Petroleum industry
Downhole pumps in the field of crude oil production offer a high degree of economic efficiency compared to traditional pumping equipment. Thanks to their easy installation and maintenance, good controllability and high efficiency under difficult pumping conditions, there has been a worldwide increase in the number of pumps. To reduce long downtimes and costs caused by premature failures, we have developed special abrasion-resistant materials for the stators of the downhole pumps. The geometries are fine-tuned to the expected geological temperatures. We offer you complete systems as well as a relining service for worn stators.
Dosing technology
In the electronics industry in particular, ever smaller components must be bonded or encapsulated. One of the main tasks of stators is therefore to convey very small quantities of various media with a high degree of repeat accuracy without dripping. Due to the composition of the materials specifically adapted to the media, our stators achieve the highest possible chemical resistance!
Construction industry
Especially in the construction industry, the screw conveyors have to convey extremely abrasive substances. Artemis offers stators of various designs with a rubber or plastic casing or slotted steel tube for retensioning to prevent wear and tear of the progressive cavity pumps as far as possible. We develop solutions for you so that we achieve an optimum service life for your progressive cavity pump!
Chemical industry
In the chemical industry, the resistance of the stator’s elastomer must meet the highest demands. Media to be pumped can be all kinds of substances, such as filter cake, which has hardly any liquid properties, sludge and many other chemical substances. Our sales teams and laboratory technicians will support you in selecting the appropriate compounds for your application. Our resistance list has proven to be a useful tool in this context.
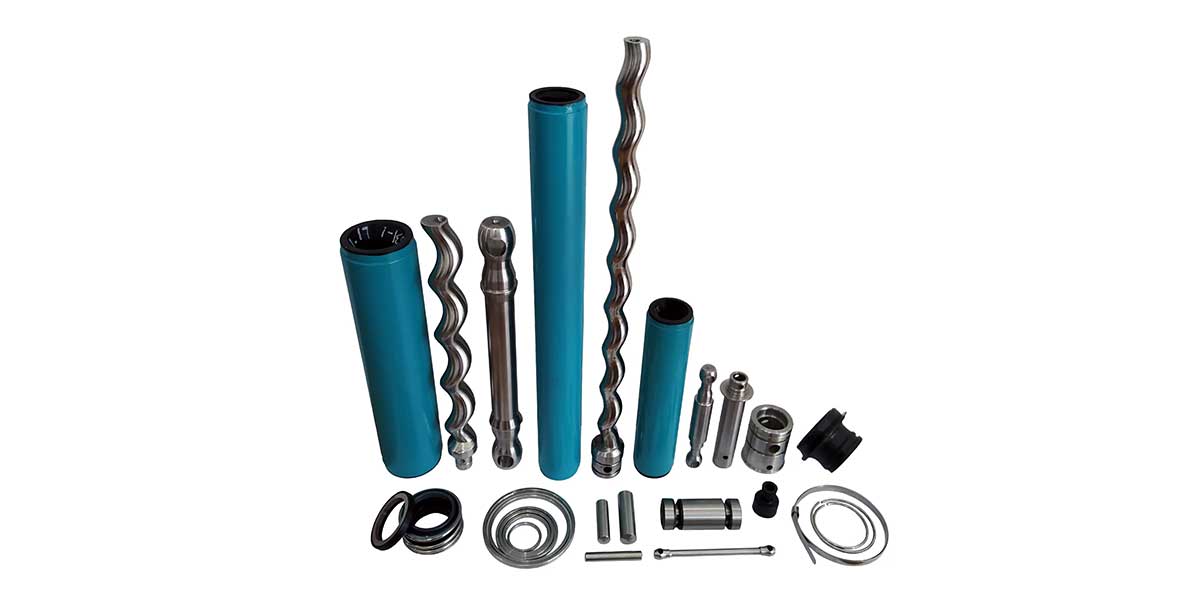
The fine art of machining ceramics
Since 2021, Kern Microtechnik GmbH’s job shop manufactures different ceramic parts which are being used in a wide variety of applications.To get more news about machining ceramics, you can visit runsom.com official website.
The ductile cutting mode, developed by Kern, is playing a vital role. Engineers and technicians, together with the customer, succeeded in generating a reliable process which provides high-quality results and zero rejects.
Many different industries, such as analytics, chemical and waveguides have been waiting for this, as have manufacturers of highly precise parts for measurement devices, jewellery, watchmaking and satellite technology for example. It’s all about the reliable manufacturing of technical ceramics like silicon carbide and aluminium oxide. The extreme hardness, stiffness, heat and chemical resistance of these materials and their excellent thermal connectivity make ceramics a very interesting material for many different applications.
However, the many advantages pose a challenge at the same time: the manufacturing process is very demanding. Also, because ceramic products need to be 100% perfect, cracks, breakoffs, or damaged material result in a failure of the part. Unlike metal, there is no protection to limit the spread of a crack. Furthermore, parts need to be manufactured to high dimensional accuracies.
Lapping, honing and grinding are established as traditional manufacturing processes, however, this limits the profiles and shapes that can be produced. Also, reliability becomes an issue as soon as contours and outlines need to be cut. This is where the new ductile cutting mode, developed by Kern engineers, comes into play. Special milling tools, with a geometrically defined cutting edge remove material from brittle ceramics with flying chips.
High-quality, high reliability
Alexander Stauder, head of applications at Kern explains: “We gain many advantages with this process – most important are the excellent quality in terms of accuracy and surface finishes and also process reliability. Depending on the quality of the ceramics, Ra/Sa roughness in the range of a few tens of nanometres and accuracies in the lower micrometre range can be achieved.”
Often it is possible to cut machining times considerably, which results in more efficiency. However, there is a rule of thumb: the larger the parts and respectively the drills and grooves are, the more it makes sense to use grinding as the first metal removal method.
Finishing is then the only thing remaining for milling, where tools are sometimes more costly. The smaller the parts and respectively the drills and grooves are, the more productive it becomes to work directly with the ductile cutting mode.
For either process, a reliable machine with highest accuracies is essential. A high stiffness and running smoothness, a spindle with a high RPM and resistance against the abrasive ceramic removal are prerequisites for working with either ductile cutting mode or grinding.

Basic Guide To CNC Machining Tolerance
NC machining refers to the use of computer programming and electromechanical equipment to automatically process metal parts (and non-metallic) as required. CNC machine tools perform all operations on the workpiece according to the program and provide us with the final product.To get more news about machining tolerances, you can visit runsom.com official website.
CNC machining refers to the use of computer programming and electromechanical equipment to automatically process metal parts (and non-metallic) as required. CNC machine tools perform all operations on the workpiece according to the program and provide us with the final product.
Although CNC machining service is very accurate in product size, it is not perfect. From the part material to the machining process used, various factors may lead to differences. Therefore, engineers assign machining tolerances to parts during the design process.
What is Machining Tolerance?
Machining tolerance, also known as dimensional accuracy, is the acceptable deviation of part size.
This is expressed as the maximum and minimum size limit of the part. If the size of the part falls between these limits, the part is considered to be within the tolerance range. However, if the size of parts exceeds these limits, these parts exceed the acceptable tolerance range and are considered unusable.
The machining tolerance usually starts with a ± symbol. For example, suppose a 2.0 "(50.8mm) high part requires a tolerance range of ± 0.005" (0.127mm). The variable height of the final part should be between 2.005 "(50.927mm) and 1.905" (48.387mm) to pass the quality inspection.
The tolerance can also be expressed in any decimal place. The more decimal places included, the tighter the tolerance. These different types of tolerances are expressed as follows:
What Are the Standard Machining Tolerances?
There is no true standard machining tolerance, mainly because different applications require different tolerances. However, some manufacturers and industry organizations have established standard tolerances they use or recommend for certain parts and materials. This is particularly true in the military and aerospace manufacturing industries.
Generally, the customer will provide the tolerance of their project to the mechanical workshop. Some mechanical workshops require customers to provide tolerances, but if not, other mechanical workshops operate according to the common tolerance list. For example, in SANS, our standard manufacturing tolerance is ± 0.004 "(0.1mm).

Sheet Metal Fabrication Services
Amid the COVID-19 crisis, the global market for Sheet Metal Fabrication Services estimated at US$15.3 Billion in the year 2022, is projected to reach a revised size of US$17.2 Billion by 2026, growing at a CAGR of 2.6% over the analysis period. To get more news about online sheet metal fabrication, you can visit runsom.com official website.
Sheet metal fabrication refers to the subtractive processing method to cut sheet metal into parts. Growth in the global market is being driven by rapid urbanization in many developing regions, and a robust trend of R&D investments in several services sectors. Increasing demand for sheet metal fabrication from a wide range of major end users such as military & defense, aerospace, automotive, oil and gas, industrial machinery, medical devices, construction, agriculture, consumer products, and electronics is expected to drive growth.
Moreover, the current focus on enhancing operational efficiency and lean manufacturing is contributing to increased demand for the process of sheet metal forming among OEMs. Innovative prefabrication techniques adopted by sheet metal fabrication service providers to meet the growing demand are expected to further drive the growth. The increasing shortage of labor could be addressed by adopting cobots in metal fabrication processes. Therefore, increasing number of metal fabrication facilities are adopting cobots to enhance operational efficiency and improve product quality.
The Sheet Metal Fabrication Services market in the U.S. is estimated at US$2.7 Billion in the year 2022. The country currently accounts for a 17.78% share in the global market. China, the world's second largest economy, is forecast to reach an estimated market size of US$6 Billion in the year 2026 trailing a CAGR of 3.4% through the analysis period. Among the other noteworthy geographic markets are Japan and Canada, each forecast to grow at 1.5% and 2% respectively over the analysis period. Within Europe, Germany is forecast to grow at approximately 1.8% CAGR while Rest of European market (as defined in the study) will reach US$6.2 Billion by the end of the analysis period.

Smart Services Identifies CNC Machining Quality Issues
A collaboration between Productive Machines (UK) and the Kistler Group allows customers in the machining segment to benefit from a full range of performance optimization services. Dynamic stiffness analysis together with force and vibration mapping are the keys to efficiently enhancing CNC machining processes and boosting productivity, in an approach based on simulations, measurements, and data analysis.To get more news about precision medical machining, you can visit runsom.com official website.
Production equipment such as machinery and robots must be maintained in good operating condition to ensure that manufacturing processes are productive, cost-efficient and highly sustainable. In the specific context of modern CNC machining, it is essential to apply, trace and adjust the right electrical and mechanical settings throughout a machine’s lifetime.
Maximizing Tool And Machine Performance
Kistler has announced the partnership with Productive Machines Ltd (UK) covering extended services to optimize machining processes, with a particular focus on milling applications. Productive Machines was founded by Dr. Erdem Ozturk, who also led the machining dynamics team at The University of Sheffield Advanced Manufacturing Research Centre (AMRC). The company supports manufacturers with dynamic analyses of CNC machining tools, as well as providing both physical and digital services to optimize NC programs.
The collaboration between Kistler and Productive Machines offers customers a range of value-added services in machine tool analysis: methods such as dynamic stiffness mapping, cutting force simulations and feed rate scheduling will help to minimize milling force spikes and maximize tool life and performance. Chatter vibrations can also be minimized by a prediction per stability map and an according adaptation of spindle speed. Another focus of the partnership is holistic optimization of CAM files as an aid to improving productivity and quality.
The physical stage of the service is performed with an impulse hammer – a device containing a piezoelectric force sensor that dynamically excites the structure under test. Resulting vibrations are measured with IEPE accelerometers from Kistler, and a modal analysis then determines the dynamic behavior of the structure (a milling machine, for example).
The partners are also offering DIGI-FORCE – a new digital service to determine key parameters of a machine setup based on machine data. Various levels of the DIGI-FORCE service are available, and it can be combined with physical measurements to obtain a complete account of machine and tool capability and performance. The DIGI-FORCE OPT service adds the FRF file data from the machine measurement to the optimized CNC program – so chatter vibrations, tool wear and machine breakdowns can be significantly decreased or even eliminated altogether.
Researchers and production engineers who opt for these services benefit from simulated force levels as the basis for optimizing their CNC machining programs – leading not only to enhanced productivity but also reduced effort for R&D and process analysis.

China cracks down on fan groups
China's increasing effortsto regulate society have led Beijing to a new target: celebrity culture and the often raucous fan groups surrounding it.To get more latest entertainment news, you can visit shine news official website.
The country's top internet watchdog has said it will bar platforms from publishing lists that rank celebrities and will also regulate the lucrative industry of fan merchandise sales.
Last week's announcement is a doubling down on Beijing’s efforts to curtail the “chaotic” influence of the entertainment industry after a series of controversies involving celebrities.
Online celebrity fan clubs have become a widespread phenomenon, with the country's "idol economy" thriving.
But they have also been criticized for their influence over minors and for deviating from the Communist Party’s desired social order.
Competing fan clubs regularly clash on social media and trade online abuse in "fandom wars" over lists that rank popular celebrities or other points of fan contention. Some spend large amounts of money to vote for their favorite stars on idol competition programs.
Although this type of fan culture has become common across Asia, in China the government is taking notice — and moving to exert its influence over what has been a largely unregulated space for digital expression.This policy is an attempt to regulate the pop culture market rather than the culture itself,” said Jin Vivian Zhan, Associate Professor of Politics at the Chinese University of Hong Kong.
“Many organizers of the fans' communities are not really fans but economic actors who seek business opportunities in supporting/cultivating idols and make profits out of it.” she said.
The internet regulator began a two-month campaign in June in an effort to address the phenomenon and on Friday it said that while it had made some progress, it would now unveil new guidelines for local authorities across the country.
Platforms will no longer be able to publish lists of popular celebrity individuals and fan groups must be regulated, the watchdog said.
It also moved to stop variety shows from charging people to vote online for their favorite acts and spoke out against enticing young fans into buying celebrity merchandise.Regulators need to "increase their sense of responsibility, mission and urgency to maintain online political and ideological security," the Cyberspace Administration of China said in a statement.
Carol Sun, a 22-year-old student from Beijing and a fan of the online sensation Xiao Zhan, told NBC News that she thinks the crackdown could help young people realize the risks in fandom culture. “Although in the long term, oversight alone is unlikely to solve the problem” she said.
Celebrities in China have access to an unrivaled base of fans, but are also no strangers to public backlash or government scrutiny.According to Reuters, in late July, around 64 Chinese celebrities attended a government-arranged course where the content included Communist Party history and the responsibilities that public figures have.
Hugely popular actress Zheng Shuang was given a $46 million tax evasion fine on Friday by Shanghai tax authorities after a probe that followed a surrogacy controversy which engulfed Shuang in January.Separately, Chinese video platforms on Friday took down films starring or directed by Zhao Wei, one of China's biggest stars, citing "relevant laws and regulations," which prompted widespread online speculation over the reason. Her name was also removed from online casting lists.
Chinese celebrities have been subjected to such treatment in the past when they have fallen foul of the authorities or public sentiment.
Archives
- All
- November 2024
- October 2024
- September 2024
- August 2024
- July 2024
- June 2024
- May 2024
- April 2024
- March 2024
- February 2024
- January 2024
- December 2023
- November 2023
- October 2023
- September 2023
- August 2023
- July 2023
- June 2023
- May 2023
- April 2023
- March 2023
- February 2023
- January 2023
- December 2022
- November 2022
- October 2022
- September 2022
- August 2022
- July 2022
- June 2022
- May 2022
- April 2022
- March 2022
- February 2022
- January 2022
- December 2021
- November 2021
- October 2021
- September 2021
- August 2021
- July 2021
- June 2021
- May 2021