More Information on Solving Helical Rotor Pump from freeamfva's blog
More Information on Solving Helical Rotor Pump
Pumping Abrasives with Progressive Cavity, Helical Rotor, Eccentric Screw Pumps. Often used to pump slurries, helical rotor pumps (also known as progressivity cavity pump, eccentric screw pump, mono pump) use a spiral rotor to move a chamber full of product through the pump. When moving slurries it is critical that the rotor wipes the rubber or elastomer stator firmly, else fine particles get between the rotor and stator and rip material out. This article discusses a major operating problem when the wrong size rotor was used in a stator.To get more news about SEEPEX Pump Parts, you can visit hw-screwpump.com official website.
Keywords: pumping abrasive, pumping slurry,progressive cavity pump, helical rotor pump, eccentric screw pump, mono pump
It’s been an absolute nightmare finding out what to do with a single stage progressive cavity pump that kept chopping out rotor and stator regularly for the past six months.
It was moving a 5%, 0.5 mm diameter sand slurry. No one knew what had changed. It had worked fine for 4 years during which time the rotor and stator was changed every 4 to 6 months. Then suddenly we were changing a rotor and stator every week or two.
What we found was that eight months earlier the supplier had recommended a change in rotor tolerance because of high process temperature. He suggested we try a thinner rotor to allow for expansion due to the temperature rise. We agreed to test it and in error the new item became the standard replacement part. New thinner rotors were brought to replenish stock.
The new rotor did not last long and a spare was installed. The spare was the thinner rotor. The rotor again did not last long and the spare was taken from store. It was a thin rotor. The spare was replenished but it was again with a thin rotor. These thin rotors kept being used at each repair.
This continued until production was severely affected. A thorough investigation highlighted the problem and it was corrected and previous bigger diameter rotors were put back into stock.
Have a very tight compression between the metal rotor and rubber stator so the rotor firmly wipes the stator and forces any fine abrasive along with the progressive cavity. We measured 0.8 mm difference in rotor diameter (nominally 50 mm diameter) between the thinnest and thickest rotor. The 80 C temperature rise would never have expanded the rotor to fill the gap created by using such a thin rotor within the stator.The pump supplier was concerned that with too much pressure between rotor and stator it was possible to rip the rubber out of the stator due to friction from the rotor. We have not experienced such failures in our processes, but I have no doubt that it can happen with certain products.
The larger 0.4 mm gap between rotor and stator let the pump pressure recirculate and squeeze the particulate into the space between rotor and stator.The rising pressure through the pump pushes and deforms the rubber in the stator. The sand trapped against the upstream curves of the rotor rip across the deformed rubber stator as the rotor turns and both are scored.
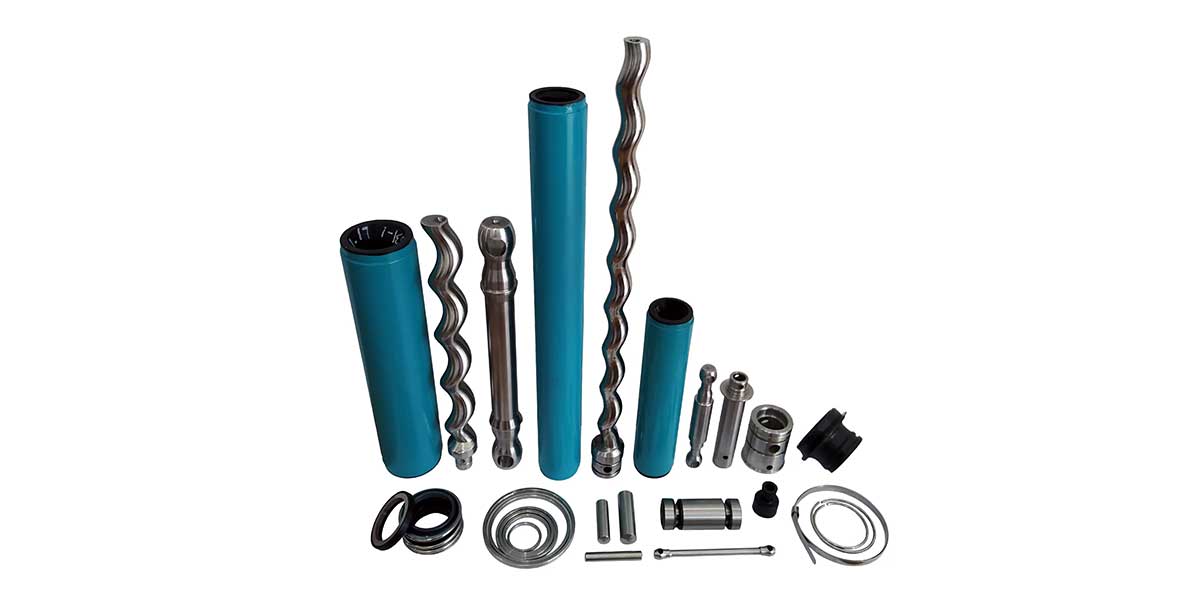
Post
By | freeamfva |
Added | Apr 13 '23 |
Tags
Rate
Archives
- All
- November 2024
- October 2024
- September 2024
- August 2024
- July 2024
- June 2024
- May 2024
- April 2024
- March 2024
- February 2024
- January 2024
- December 2023
- November 2023
- October 2023
- September 2023
- August 2023
- July 2023
- June 2023
- May 2023
- April 2023
- March 2023
- February 2023
- January 2023
- December 2022
- November 2022
- October 2022
- September 2022
- August 2022
- July 2022
- June 2022
- May 2022
- April 2022
- March 2022
- February 2022
- January 2022
- December 2021
- November 2021
- October 2021
- September 2021
- August 2021
- July 2021
- June 2021
- May 2021
The Wall