freeamfva's blog
Seamless vs. Welded Pipes: A Comparative Study
Pipes are integral to numerous industries, with their applications ranging from the transportation of water, oil, gases to construction. There are two primary types of pipes - seamless and welded, each with its unique manufacturing process, characteristics, and uses.To get more news about Steel pipe, you can visit friend-steelpipes.com official website.
Manufacturing Process
Seamless Pipes are made from a solid round steel billet heated and stretched out over a form. The process involves piercing through the center with a die and mandrel, which increases the inside diameter and reduces the outside diameter.
On the other hand, Welded Pipes are made by cold forming flat strips, sheets, or plates into a round or circular shape by a roller or plate bending machine. The pipe is then welded with or without filler material using a high-energy source.
Strength and Length
Seamless pipes can withstand more pressure and load as there is no weak seam. However, they are relatively shorter in length due to manufacturing difficulties. Welded pipes, believed to withstand 0% less pressure and load compared to seamless pipes, can be manufactured in long continuous lengths.
Size and Corrosion Resistance
Seamless pipes are usually manufactured for a nominal size of 4 inches or less. They are less prone to corrosion, making them more corrosion-resistant. Conversely, welded pipes do not have any size restriction on production, but their weld areas are more prone to corrosion attacks, which means less corrosion resistance.
Surface Quality and Economy
Seamless pipes have a rough surface due to the extrusion process, while welded pipes have a smooth high-quality surface. Seamless pipes are costlier than welded pipes due to their complex production process and long procurement lead time.
Conclusion
In summary, both seamless and welded pipes have their advantages and disadvantages. The choice between the two depends on the specific requirements of the application. Seamless pipes offer higher strength and better surface finish but are more expensive than welded pipes.
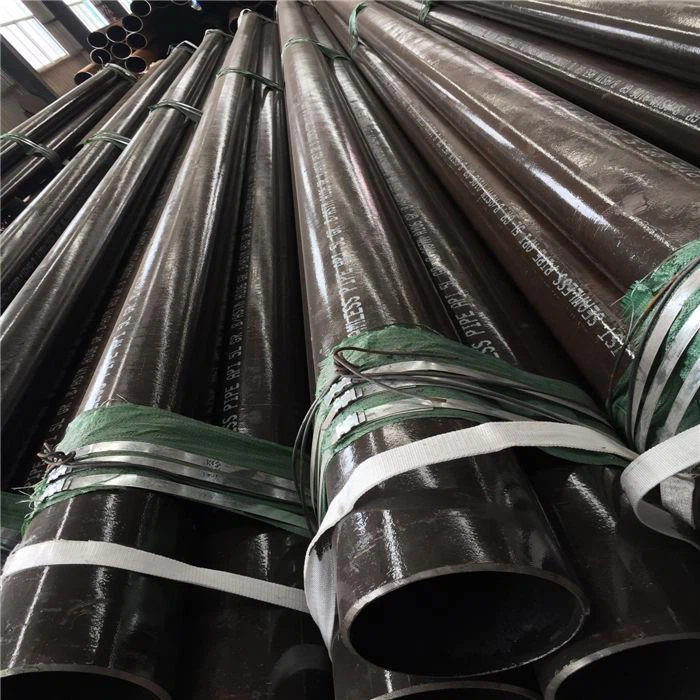
The Essentiality of Investing in Quality Women’s Dance Shoes
Dance, an art form that transcends cultural boundaries, requires not only skill and passion but also the right equipment. Among these, dance shoes hold a paramount position. They are the vital link between the dancer and the dance floor1. This article explores why investing in quality women’s dance shoes is essential.To get more news about Women's Dance Shoes, you can visit https://www.changxshoes.com official website.
Quality Over Quantity
Quality dance shoes are lightweight, comfortable, flexible, and made of real suede or leather. They provide your foot with more freedom of movement than regular shoes while keeping the heel “locked” in place. The soles of dance shoes are designed to give you just the right amount of slip-and-grip on the dance floor while allowing your foot to pivot freely. This balance prevents knee damage that can occur from wearing inappropriate footwear.
The Perfect Fit
A good dance shoe should fit like a glove. There should be no wiggle room as they will stretch a bit once you start dancing. A snug fit allows your foot to connect better with the floor, giving you more control over your movement, balance, and spins. It significantly reduces your fear of slipping and falling.
Style and Substance
The market offers a wide array of styles catering to different dance forms. From ballroom to Latin, there’s a shoe for every dancer. For instance, women’s ballroom dance shoes come in various styles like Style 1012, which is perfect for beginner ballroom dancers who want feminine beauty and princess-style looks.
Care and Maintenance
To ensure longevity, it’s crucial to take care of your dance shoes properly. Shoe polish works great for leather shoes, while soap and water can clean satin, mesh, and sparkle net. Suede bottom shoes can wear out quickly if worn on the street. Hence, it’s best to wear them on dance floor surfaces only.
Conclusion
Investing in quality women’s dance shoes is not an extravagance but a necessity. They make a significant difference in a dancer’s performance by providing comfort, ensuring safety, and enhancing style. So next time you’re shopping for dance shoes, remember - quality is essential!

Top 10 Women’s Dance Shoes for Every Style
Choosing the right dance shoe can make all the difference in your performance. Here are the top 10 women’s dance shoes for every style:To get more news about Women's Dance Shoes, you can visit https://www.changxshoes.com official website.
Ballet Flats: Ballet flats are a staple for any dancer. They are lightweight, flexible, and provide excellent support for the foot.
Jazz Shoes: Jazz shoes are perfect for jazz dance styles. They offer flexibility and support, allowing dancers to perform complex footwork with ease.
Tap Shoes: Tap shoes are designed with metal plates on the soles to create a distinctive sound. They are essential for tap dancing.
Ballroom Shoes: Ballroom shoes are elegant and stylish, designed for dances like the waltz, tango, and foxtrot. They typically have a suede sole for smooth movement on the dance floor.
Latin Dance Shoes: Latin dance shoes are similar to ballroom shoes but have a higher heel to accentuate the dancer’s movements.
Hip Hop Sneakers: Hip hop sneakers are designed for hip hop and street dance styles. They offer excellent support and cushioning for high-impact moves.
Belly Dance Shoes: Belly dance shoes are lightweight and flexible, allowing dancers to move their feet freely.
Contemporary Dance Shoes: Contemporary dance shoes provide protection while allowing dancers to connect with the floor.
Pointe Shoes: Pointe shoes are used in ballet for dances that require the dancer to stand on their toes.
Irish Dance Shoes: Irish dance shoes, also known as ghillies, are used in traditional Irish dance. They are soft and flexible, allowing dancers to perform intricate footwork.
Choosing the right dance shoe is crucial for any dancer. It can enhance your performance, provide necessary support, and protect you from injuries. Remember to consider your dance style, comfort, and fit when choosing your dance shoes.

Understanding Controlled Expansion Alloys
Controlled Expansion Alloys, also known as expansion alloys or thermal expansion alloys, are precision alloys with unique thermal expansion characteristics. These alloys are primarily composed of iron, nickel, and sometimes cobalt2, and are used in applications where the thermal size change of the metal must be considered in the design.Get more news about Controlled Expansion Alloy,you can vist our website!
The alloys classified in this category include Alloy , Alloy 46, Alloy 48, Alloy 52, Kovar®, Invar®, and Super Invar3. These alloys are found in a broad variety of applications where thermal changes of a metal must be factored into the design of a component3. They are typically useful when forming a hermetic seal with glass or ceramic or when a specific expansion must be met over a certain temperature range.
Alloy 42 is a controlled expansion alloy consisting of 41% nominal nickel, balance iron. It is used in a wide variety of electronic applications, lead frames, especially for glass and ceramic seals3. Alloy 46 contains 46% nickel with the balance iron and is used in applications that require glass and ceramic seals.
Alloy 48 consists of approximately 48% nickel and the balance iron. This binary nickel-iron alloy is applicable to a wide variety of electronic applications that require a low coefficient of expansion at 400°C for glass-to-metal seals in soft lead or soda lime glasses.
Alloy 52 is another controlled expansion alloy consisting of 50.5% nominal nickel, balance iron; used in a wide variety of electronic applications especially for glass seals3. Invar® is a low expansion alloy consisting of nominal 36% nickel; balance iron. This controlled expansion alloy is known for its rate of thermal expansion that is approximately one-tenth of carbon steel at ambient temperatures up to 400°F3.
These characteristics have made these alloys contenders for many applications where dimensional changes due to temperature variations must be minimized. With more than 160 years materials expertise, companies like Sandvik provide tailor-made components made from Osprey® controlled expansion (CE) alloys.
In conclusion, Controlled Expansion Alloys play an essential role in various industries due to their unique thermal expansion properties. Their use in electronic applications and their ability to form hermetic seals with glass or ceramic make them invaluable in today’s technology-driven world.
The Power Window Switch: A Key Component in Modern Vehicles
The power window switch is an integral part of the modern vehicle. It is the device that controls the up and down movement of the car’s windows. This seemingly simple device plays a crucial role in ensuring comfort and convenience for the vehicle’s occupants.Get more news about power window switch supplier,you can vist our website!
The power window switch operates on a simple principle. When you press the button, it sends an electrical signal to the window motor, which then moves the window up or down. The switch is usually located on the door panel for easy access.
One of the main advantages of power windows over manual windows is convenience. With power windows, you can control all windows in the car from the driver’s seat. This is particularly useful when you need to open or close windows while driving.
However, like any other component in a vehicle, the power window switch can also experience problems. Common issues include a slow-moving window, a window that doesn’t stay up, or a switch that doesn’t respond at all. These problems can be caused by various factors such as a blown fuse, a faulty motor, or a worn-out switch.
When faced with such issues, it’s important to get them fixed promptly. Ignoring them could lead to more serious problems down the line. For instance, a window that doesn’t close properly could make your car an easy target for thieves.
In conclusion, the power window switch is more than just a button on your door panel. It’s a key component that contributes to your vehicle’s functionality and your overall driving experience. So next time you roll down your window to enjoy the breeze, remember the humble power window switch that made it possible.
The Power of Suction: Two Stage Rotary Vane Vacuum Pumps
In the realm of industrial machinery, the Two Stage Rotary Vane Vacuum Pump stands out as a powerful and versatile tool. Its unique design and operation make it an essential component in various applications, from refrigeration systems to scientific research.Get more news about Two Stage Rotary Vane Vacuum Pump Seller,you can vist our website!
A Two Stage Rotary Vane Vacuum Pump operates on a simple yet effective principle. It consists of a rotor with vanes, housed inside a cylindrical chamber. As the rotor spins, the vanes slide in and out, creating chambers that suck in and expel air. This action creates a vacuum.
The “two-stage” in its name refers to the pump’s operation. In the first stage, the pump creates a moderate vacuum by removing most of the air from the system. In the second stage, it removes the remaining air to create a high vacuum. This two-stage process allows the pump to achieve a deeper vacuum than single-stage pumps.
One of the key advantages of Two Stage Rotary Vane Vacuum Pumps is their efficiency. They can achieve higher vacuum levels and have faster pumping speeds compared to other types of vacuum pumps. This makes them ideal for applications that require high vacuum levels or rapid evacuation of air.
Another benefit is their versatility. These pumps can handle both dry and wet gases, making them suitable for a wide range of applications. They are commonly used in industries such as food processing, pharmaceuticals, and electronics manufacturing.
Despite their powerful performance, Two Stage Rotary Vane Vacuum Pumps are known for their compact design and ease of maintenance. Their simple construction makes them easy to service and repair, reducing downtime and maintenance costs.
In conclusion, the Two Stage Rotary Vane Vacuum Pump is a testament to the power of engineering and design. Its ability to create high vacuums efficiently and reliably makes it an invaluable tool in many industries. As technology continues to advance, we can expect these pumps to become even more efficient and versatile, further solidifying their place in the industrial landscape.
Harnessing the Power of TURBOHEAT
TURBOHEAT, a name that has become synonymous with innovation and efficiency in heating technology, is revolutionizing the way we heat our spaces. Whether it’s a cozy living room or a spacious office, TURBOHEAT has proven to be a game-changer.Get more news about TURBOHEAT,you can vist our website!
The secret behind TURBOHEAT’s success lies in its unique Micro-Ceramic Technology. This technology transforms cold, chilly air into warm, soothing heat, providing comfort during those cold winter months. The powerful heating capacity of TURBOHEAT can warm up to 50 square feet, making it an ideal choice for various spaces.
One of the standout features of TURBOHEAT is its compact size. Despite its small form factor, it doesn’t compromise on heat output. It plugs directly into the wall outlet, saving valuable floor space and eliminating the need for messy wires.
TURBOHEAT is not just about warmth; it’s about personalized comfort. With an adjustable thermostat, users can set the temperature to their exact comfort zone. Moreover, TURBOHEAT operates quietly, ensuring that your peaceful moments remain undisturbed.
In addition to its impressive features, TURBOHEAT is also cost-effective. It runs for just pennies a day, making it an economical choice for many households.
TURBOHEAT is not only limited to homes. Its portability makes it perfect for travel, offering quick and cozy comfort wherever you go. Whether you’re in your RV or at your office, TURBOHEAT ensures you stay warm and comfortable.
In conclusion, TURBOHEAT is more than just a space heater; it’s a testament to how innovative technology can enhance our daily lives. By delivering powerful heating in a compact design, TURBOHEAT has truly redefined what we can expect from our heating systems.
Auto Shrink Wrap Machine: A Comprehensive Overview
Auto shrink wrap machines are a type of packaging machinery that are used to wrap products in a layer of plastic film. This process is known as shrink wrapping and is used to protect products from damage during shipping and handling. In this article, we will provide a comprehensive overview of auto shrink wrap machines, including their features, benefits, and applications.Get more news about Auto Shrink Wrap Machine,you can vist our website!
What is an Auto Shrink Wrap Machine?
An auto shrink wrap machine is a type of packaging machinery that is used to wrap products in a layer of plastic film. This process is known as shrink wrapping and is used to protect products from damage during shipping and handling. Auto shrink wrap machines are fully automated and can detect a product, seal, and shrink without human operation 1. These machines have infeed and exit conveyors, which need to be loaded and unloaded as the line is in process 1. The term “automatic shrink wrap machine” is a general term that can refer to many different styles and functions of devices 1.
Features of Auto Shrink Wrap Machines
Auto shrink wrap machines come with a variety of features that make them ideal for different applications. Some of the most common features include:
Auto shrink wrap machines offer several benefits over manual shrink wrapping. Some of the most significant benefits include:
Increased efficiency: Auto shrink wrap machines are fully automated, which means they can wrap products faster than manual methods.
Consistency: Auto shrink wrap machines provide consistent results every time, which helps ensure product quality.
Reduced labor costs: Auto shrink wrap machines require less labor than manual methods, which can help reduce labor costs.
Improved safety: Auto shrink wrap machines are designed with safety features that help prevent accidents.
Applications of Auto Shrink Wrap Machines
Auto shrink wrap machines are used in a variety of industries for different applications. Some of the most common applications include:
Food packaging: Auto shrink wrap machines are used to package food products such as meat, poultry, seafood, and produce.
Beverage packaging: Auto shrink wrap machines are used to package beverages such as water bottles, soda cans, and juice boxes.
Pharmaceutical packaging: Auto shrink wrap machines are used to package pharmaceutical products such as pills and capsules.
Consumer goods packaging: Auto shrink wrap machines are used to package consumer goods such as electronics, toys, and games.
Conclusion
Auto shrink wrap machines are an essential piece of equipment for many industries. They offer several benefits over manual methods, including increased efficiency, consistency, reduced labor costs, and improved safety. With their many features and applications, auto shrink wrap machines are an excellent investment for any business looking to improve its packaging process.
The Precision and Power of Laser Cutting Lines
Laser cutting technology has revolutionized the manufacturing industry, providing unprecedented levels of precision and efficiency. At the heart of this technology is the laser cutting line, a tool that has transformed the way we cut and shape materials.Get more news about laser cutting line,you can vist our website!
The laser cutting line is a high-powered beam of light, concentrated to a tiny spot with immense heat. This heat vaporizes the material, creating a cut with remarkable precision. The laser’s intensity can be adjusted to cut through various materials, from delicate fabrics to robust metals.
One of the key advantages of laser cutting lines is their precision. Traditional cutting methods often leave rough edges or inaccuracies, but laser cutting lines produce clean, smooth cuts every time. This precision is particularly beneficial in industries where minute details matter, such as electronics or aerospace engineering.
Another significant advantage is the speed at which laser cutting lines operate. Traditional methods can be time-consuming, especially for complex designs. However, laser cutting lines can quickly trace out intricate patterns, significantly reducing production times.
Moreover, laser cutting lines offer flexibility. They can cut almost any material and are not limited by shape or size. This versatility makes them ideal for custom jobs or small production runs where traditional methods may not be feasible.
Despite these advantages, there are some considerations to keep in mind when using laser cutting lines. Safety is paramount as the high-powered lasers can cause severe burns if not handled correctly. Additionally, the initial cost of laser cutting equipment can be high, although this is often offset by the increased efficiency and precision it offers.
In conclusion, laser cutting lines have transformed manufacturing processes with their precision, speed, and flexibility. As technology continues to advance, we can expect even greater capabilities from these powerful tools.
Understanding the Importance of Undercarriage Parts
The undercarriage of a machine, vehicle, or aircraft is a fundamental component that significantly influences its performance, durability, and overall operational efficiency. This article aims to shed light on the importance of undercarriage parts and their role in ensuring the smooth functioning of various machines.Get more news about Undercarriage Parts,you can vist our website!
What are Undercarriage Parts?
The undercarriage, often referred to as the ‘running gear’, comprises several parts including tracks, track chains, rollers, idlers, sprockets, and more. These parts work in unison to support the machine, provide traction, and absorb shocks and impacts during operation.
The Role of Undercarriage Parts
Each part of the undercarriage plays a crucial role. The tracks provide grip and stability on different terrains. The track chains connect the tracks and help in transferring power from the engine to the tracks. Rollers and idlers guide the track over the terrain and absorb shocks, while sprockets engage the track chain to drive the machine forward.
Maintenance of Undercarriage Parts
Proper maintenance of undercarriage parts is essential for prolonging their lifespan and ensuring optimal machine performance. Regular inspections can help identify wear and tear early on, allowing for timely replacements or repairs. Lubrication is also crucial to reduce friction between moving parts and prevent premature wear.
Choosing Quality Undercarriage Parts
When it comes to selecting undercarriage parts, quality should never be compromised. High-quality parts offer better performance, durability, and cost-effectiveness in the long run. It’s advisable to choose parts from reputable manufacturers who provide warranties and after-sales service.
Conclusion
In conclusion, undercarriage parts are vital components that contribute significantly to the performance and longevity of machines. By understanding their importance and ensuring their proper maintenance, one can optimize machine performance and achieve operational efficiency.
Archives
- All
- March 2025
- February 2025
- January 2025
- December 2024
- November 2024
- October 2024
- September 2024
- August 2024
- July 2024
- June 2024
- May 2024
- April 2024
- March 2024
- February 2024
- January 2024
- December 2023
- November 2023
- October 2023
- September 2023
- August 2023
- July 2023
- June 2023
- May 2023
- April 2023
- March 2023
- February 2023
- January 2023
- December 2022
- November 2022
- October 2022
- September 2022
- August 2022
- July 2022
- June 2022
- May 2022
- April 2022
- March 2022
- February 2022
- January 2022
- December 2021
- November 2021
- October 2021
- September 2021
- August 2021
- July 2021
- June 2021
- May 2021