User blogs
Tag Search
Tag search results for: "screw pump stator"

How It Works: Rotary Screw Vacuum Pumps
Though the rotary screw vacuum pump may not have been around for as long as other vacuum technologies (such as liquid ring vacuum pumps), it nevertheless has become one of the most frequently used technologies in industrial vacuum applications today.To get more news about SEEPEX Pump Parts, you can visit hw-screwpump.com official website.
How Do Screw Pumps Work?
Rotary screw pumps are positive displacement pumps that consist of two mating screw rotors that rotate in opposite directions; this rotation is what moves the trapped air/gas along the length of the screws. As the trapped gas moves along the screws, it becomes compressed and is eventually discharged on the opposite end. It’s important to note that these vacuum pumps are designed to have no metal-to-metal contact within the pump housing, which results in minimal wear on the pump and less equipment overhauls.
Screw pumps can be either oil-sealed or dry. Oil-sealed screw pumps use oil for lubrication, sealing, and cooling purposes; they are ideal for rough vacuum applications that have no clean vacuum requirements, including woodworking and plastics. Dry screw pumps do not use oil/lubricant in the chamber. Rather, these are typically air-cooled and are free of any oil emissions, and can also achieve higher vacuum than oil-sealed screw pumps.
A variety of applications can benefit from using screw pumps, including woodworking, packaging, cleaning and drying, and pick and place.If there is one thing that we like seeing around here, it’s cool videos that highlight the ways mankind has developed to machine metals into the shapes and sizes that are needed for different jobs. When it comes to cars, some of the neatest looking parts are inside the cases of superchargers. There’s the cool looking straight or twisted rotors of a Roots style blower and then there’s the hypnotic screw supercharger that takes the root concept and makes it more efficient and effective. Now, these designs were not initially developed for use on engines and it took decades and decades to adapt them to help making horsepower. The screw and Roots blower were designed to be used as air pumps for things like blast furnaces, mines, and other occupational and industrial needs.
Turns out, they are still used heavily in these occupational and industrial applications and that means that they need to be produced in a massive range of sizes. That is exactly what you are going to see in this video. You’ll see rotors and screws that look like something that might be found on a big engine and then you will see stuff that seems to belong on a locomotive, ship, or other mondo spot. Hell, look at the photo above and this guy checking a set of screws that are bigger than he is!
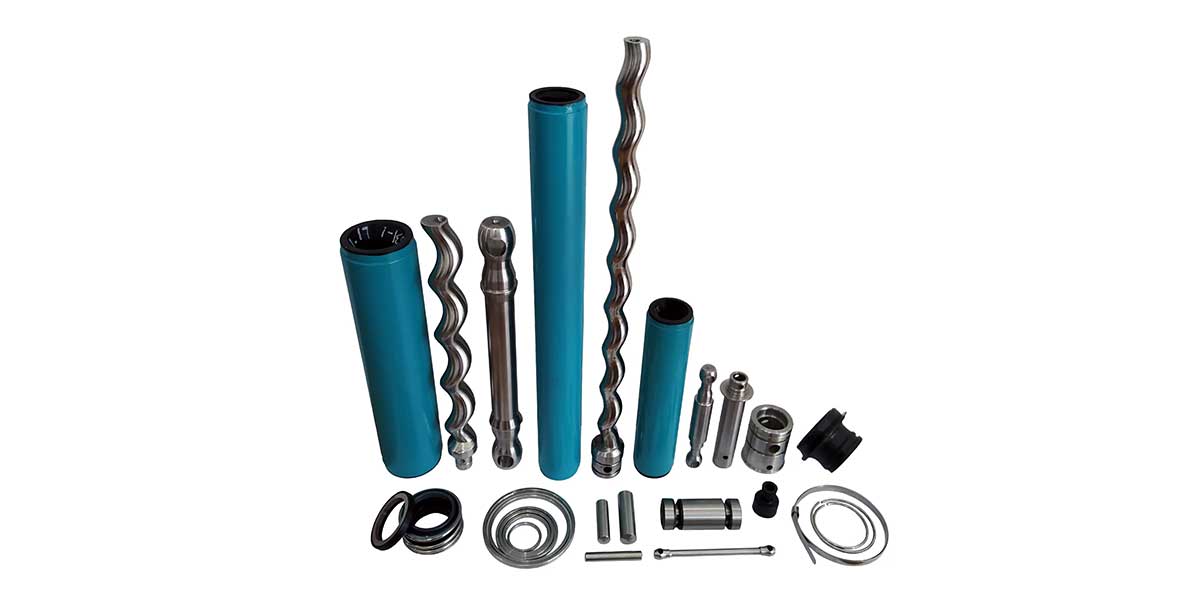

What are the reasons for the damage to the stator of the progressive cavity pump?
As one of the vulnerable parts of the progressive cavity pump, the service life of the stator has always been one of our focus. Next, I will explain several common causes of stator damage:To get more news about screw pump stator, you can visit hw-screwpump.com official website.
The most common is wear and tear, and there is the quality problem of the product itself: degumming. The wear is divided into natural wear and unnatural wear.
1. Wet abrasive wear is a condition of particle wear, that is, the conveyed medium contains particles, and there is a liquid medium between the abrasive particles and the rubber.
2.Fatigue wear is caused when the friction and contact stress between the stator rubber and the blunt mating surface of the rotor are not too large. This kind of wear is similar to abrasive wear in many aspects. Some scholars regard fatigue wear as a form of abrasive wear, that is, blunt abrasive wear. But compared with abrasive wear, fatigue wear is a low-strength wear.
Erosion wear is also known as erosion wear. This wear occurs due to the liquid flow between the screw pump rotor and stator. This type of wear is one of the main forms of wear during the normal operation of the screw pump.
Most of the unnatural wear and tear are caused by improper operation. At this time, we need to investigate the cause by ourselves. You can refer to the following knowledge points:
1. Check the pressure of the screw pump, whether the outlet valve is fully opened, and it is forbidden to close the valve at the outlet of the screw pump to adjust the flow rate and remove any blockage of the outlet pipe.
2. Check whether there are other foreign objects in the pump, remove the foreign objects, and repair the defective parts.
3. If the pump is running dry or semi-dry, check whether there is enough medium in the suction pool.
5. Check the temperature of the medium. If the stator is delayed for too long, the stator sticks to the rotor, and the stator may burn out.
6. If the diameter of the solid is too large, reduce the speed of the pump and install a proper water inlet filter.
7. The medium is solidified at the lowest temperature limit and the medium is heated.
8. When the pump is out of service, the hard solid deposits fill the pump, and the necessary disassembly and cleaning should be carried out immediately.
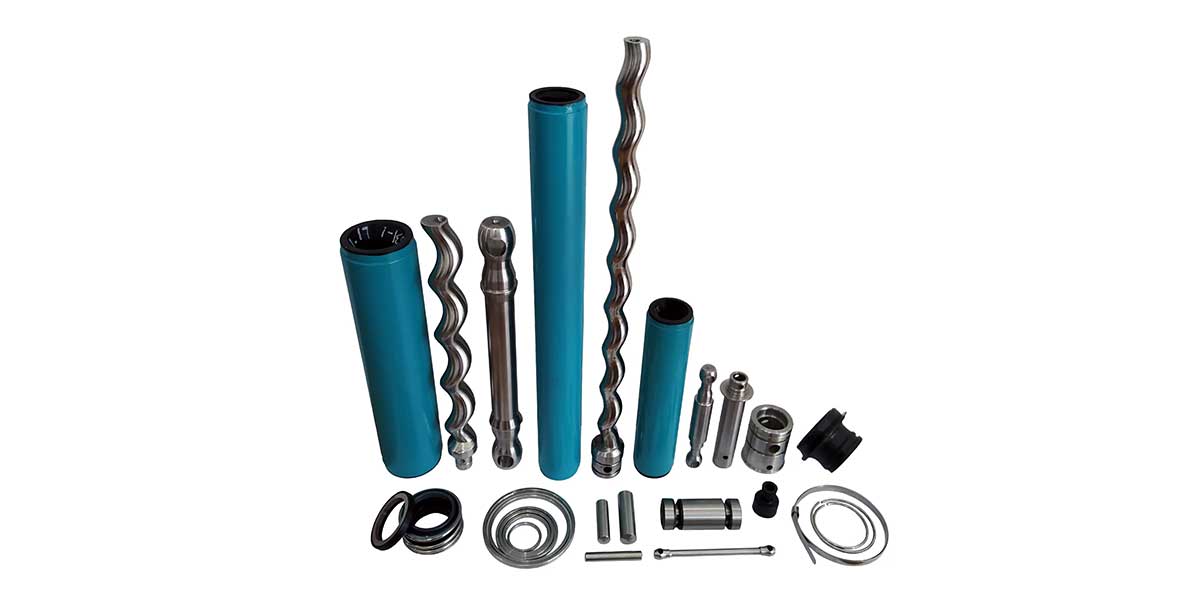

What is a screw pump stator?
The stator is a crucial component of a screw pump, and it is responsible for creating the chambers that move the fluid through the pump. It is a stationary cylinder with an internal helical profile that matches the rotor’s screw thread. The rotor rotates inside the stator, and the screw thread forms a series of chambers that trap and move the fluid from the pump inlet to the outlet.To get more news about SEEPEX Pump Parts, you can visit hw-screwpump.com official website.
The geometry of the stator’s internal profile is critical to the pump’s performance. It should be closely matched to the rotor’s helical screw thread to minimize clearance between the two components. The clearance should be minimal to ensure that the fluid is effectively trapped and moved along the screw thread without any leakage.
The stator’s material is also essential to the pump’s performance and longevity. Stator materials should have high wear resistance, corrosion resistance, and mechanical strength. Common materials used for stator construction include rubber, elastomers, and various polymers.
The stator’s design also affects the pump’s performance. For example, some screw pumps have stators with an elongated profile, while others have a shorter profile. Longer profiles tend to generate higher pressures, while shorter profiles tend to generate higher flow rates.
Another critical factor that affects the pump’s performance is the stator’s surface finish. The surface finish should be smooth to minimize friction between the stator and rotor, which can lead to wear and reduced performance.
The stator’s size also affects the pump’s performance. Generally, larger stators generate higher pressures, while smaller stators generate higher flow rates. However, the stator size should be optimized to balance performance and efficiency.
Proper maintenance and care of the stator can ensure optimal pump performance and longevity. Regular cleaning, inspection, and replacement of worn or damaged stators can help extend the pump’s lifespan and prevent downtime.
In conclusion, screw pump stator is a critical component of a screw pump. Its geometry, material, design, surface finish, and size all affect the pump’s performance and longevity. Proper maintenance and care of the stator can ensure optimal pump performance and prevent downtime.
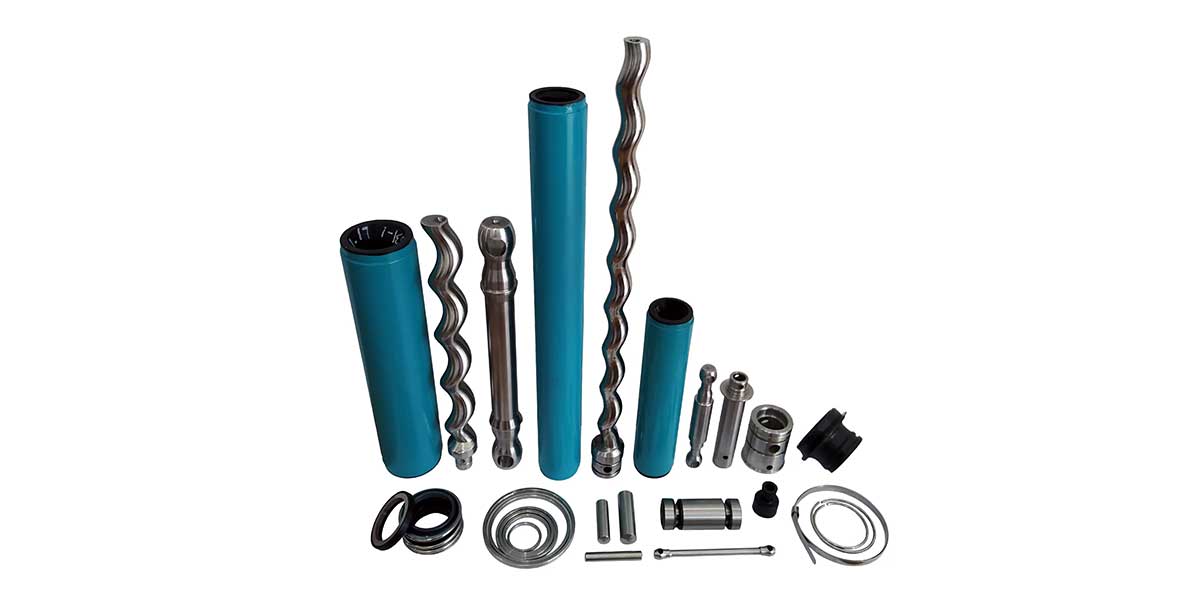

Screw Pump Rotors: A Comprehensive Overview
Screw pump rotors are the heart of screw pumps, and they play a crucial role in ensuring the smooth and efficient operation of these pumps. In this article, we will provide a comprehensive overview of screw pump rotors, including their types, features, and applications.To get more news about screw pump stator, you can visit hw-screwpump.com official website.
Types of Screw Pump Rotors
Screw pump rotors can be broadly categorized into two types: single-screw rotors and twin-screw rotors.
Single-screw rotors consist of a single helical screw that rotates inside a stator. These rotors are commonly used in applications where high pressure and low flow rates are required, such as in oilfield production and drilling, as well as in the food and beverage industry.
Twin-screw rotors consist of two intermeshing helical screws that rotate inside a stator. These rotors are commonly used in applications where higher flow rates and lower pressures are required, such as in the chemical and pharmaceutical industries.
Screw pump rotors are an essential component of screw pumps, and they offer several features that make them stand out from other pump types. They are efficient, produce low shear, are self-priming, and can handle high viscosity fluids, making them suitable for a wide range of applications. With their use in various industries such as oil and gas, chemical and pharmaceutical, food and beverage, and wastewater treatment, screw pump rotors play a crucial role in many industrial processes.
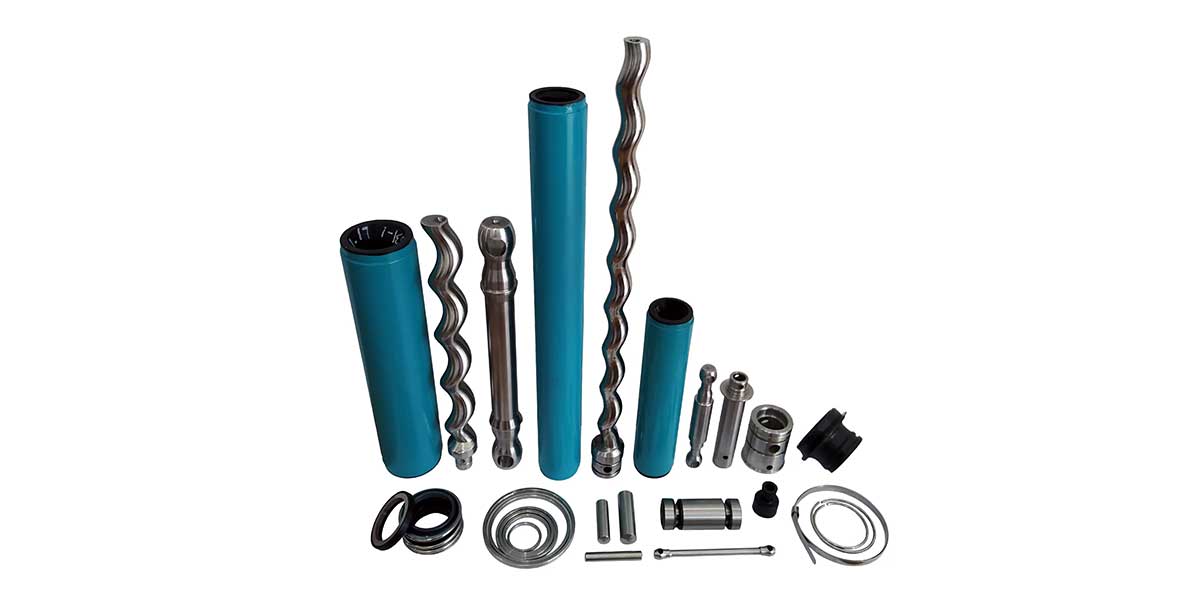

What are rotor stator pumps, and how do they work?
Rotor Stator pumps are progressive cavity pumps - a type of positive displacement pump. They can be used for pumping various viscous and abrasive fluids. To get more news about SEEPEX Pump Parts, you can visit hw-screwpump.com official website.
The fixed stator and the rotating component, the rotor, are the yin and yang of progressive cavity pumps. The rotor is the spiral steel shaft that creates conveying chambers of the inner outline of the rubber tube. Stators are metal tubes with internally molded cavities made of synthetic or natural rubber.
When the rotor is triggered, the conveying chambers move in the direction of flow. This is how the constant flow of material is achieved. The rotor takes a form which resembles a corkscrew, which, combined with the off-center rotary motion, gave its alternative name: eccentric screw pump.
2. What are rotor stator pumps used for?
Various industries use progressive cavity pumps. Putzparts is specialised in rotor stators for the construction and refractory industry to pump screed, mortar, grout, gypcrete, plaster and fireproofing cement.
Rotor stators also cater to wood processing and cellulose production, the chemical industry, the petroleum industry, domestic and industrial sewage, and low flow, high head, and agricultural water pumping.
3. What are the relevant factors when choosing the rotor stator?
Size, diameter, grain of the material, and the flow rate you want to achieve
You will want to choose your rotor stator based on its size and diameter, depending on the grain of your material and your desired flow rate. Different rotor stator pumps to suit different materials and purposes and achieve different pumping results. Different flow rates and pressure stabilities are achieved by varying designs of screw pumps.
4. Maintenance-free or clampable rotor stators?
Maintenance-free stators are more user-friendly. They can be used directly after being installed in the machine. They have unslotted steel tubes as outer casings. This means they allow for constant delivery pressure and support a hassle-free process.
Clampable stators are clamped according to material and grain size. They come in two types: stators with built-in tensioning clamps and slotted stators that are provided with an external tensioning strip.
Both transport diverse materials smoothly, continuously and with minimum pulsation. Pumps which require clamping have an integrated clamping bar or a grooved stator for the clamp, with or without an additional separate clamp. When the delivery pressure drops, the stators must be retightened.
5. How to choose the right shore for your rotor stator?
The shore is very significant: the smaller the number of the shore, the softer is the rubber. We recommend a soft rubber if you pump material with sharp aggregates, as they wear out less quickly.
6. Does Putzparts supply high-quality rotor stator pumps?
Putzparts rotor stators are made in Germany. Our high alloyed steel rotors are never hollow. We use precisely drilled, high-quality steel for long-lasting rotors.
Our stators use high-endurance rubber, which makes them long-lasting, reliable, and supportive of a solid, consistent pumping experience.
7. Can I use the pumps for different machines?
We provide Rotor Stator Pumps for various machines by Putzmeister, PFT, M-Tec, Uelzener, Turbosol, Mai, Utiform, Inotec, Imer, Brinkmann and many more. Many machines use the same rotor stator types.
For plaster, the most popular pump is the D6-3, which has a solid output of 30 litres per min at 400 rpm. If you need more, you can go with the D8-2, which has more output at 66 litres per minute than any other D-pump.
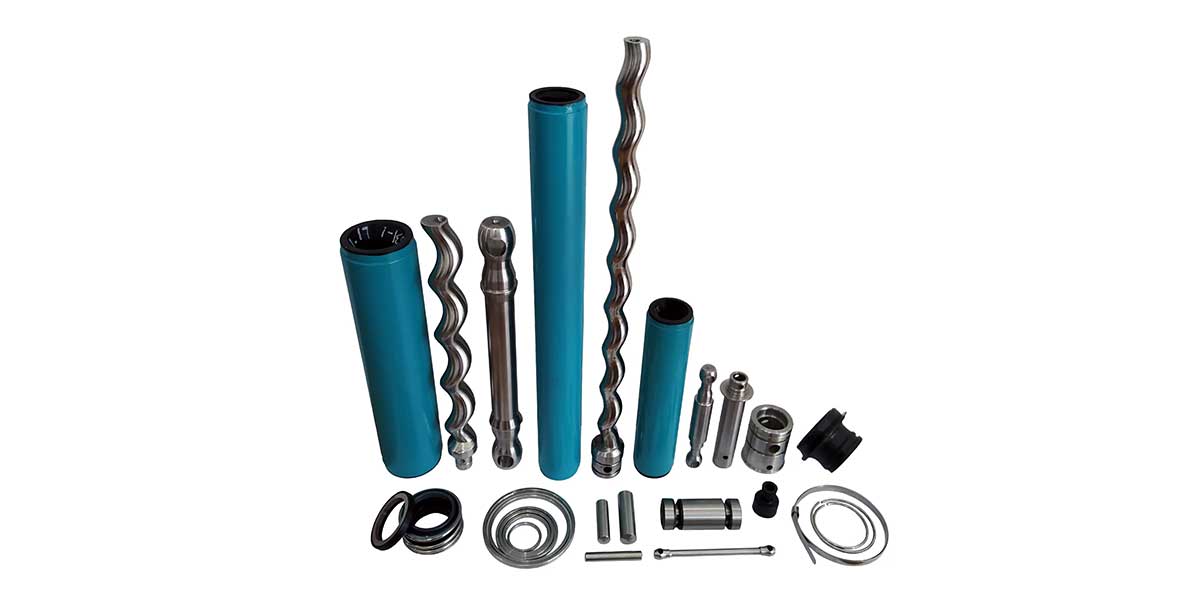

More Information on Solving Helical Rotor Pump
Pumping Abrasives with Progressive Cavity, Helical Rotor, Eccentric Screw Pumps. Often used to pump slurries, helical rotor pumps (also known as progressivity cavity pump, eccentric screw pump, mono pump) use a spiral rotor to move a chamber full of product through the pump. When moving slurries it is critical that the rotor wipes the rubber or elastomer stator firmly, else fine particles get between the rotor and stator and rip material out. This article discusses a major operating problem when the wrong size rotor was used in a stator.To get more news about SEEPEX Pump Parts, you can visit hw-screwpump.com official website.
Keywords: pumping abrasive, pumping slurry,progressive cavity pump, helical rotor pump, eccentric screw pump, mono pump
It’s been an absolute nightmare finding out what to do with a single stage progressive cavity pump that kept chopping out rotor and stator regularly for the past six months.
It was moving a 5%, 0.5 mm diameter sand slurry. No one knew what had changed. It had worked fine for 4 years during which time the rotor and stator was changed every 4 to 6 months. Then suddenly we were changing a rotor and stator every week or two.
What we found was that eight months earlier the supplier had recommended a change in rotor tolerance because of high process temperature. He suggested we try a thinner rotor to allow for expansion due to the temperature rise. We agreed to test it and in error the new item became the standard replacement part. New thinner rotors were brought to replenish stock.
The new rotor did not last long and a spare was installed. The spare was the thinner rotor. The rotor again did not last long and the spare was taken from store. It was a thin rotor. The spare was replenished but it was again with a thin rotor. These thin rotors kept being used at each repair.
This continued until production was severely affected. A thorough investigation highlighted the problem and it was corrected and previous bigger diameter rotors were put back into stock.
Have a very tight compression between the metal rotor and rubber stator so the rotor firmly wipes the stator and forces any fine abrasive along with the progressive cavity. We measured 0.8 mm difference in rotor diameter (nominally 50 mm diameter) between the thinnest and thickest rotor. The 80 C temperature rise would never have expanded the rotor to fill the gap created by using such a thin rotor within the stator.The pump supplier was concerned that with too much pressure between rotor and stator it was possible to rip the rubber out of the stator due to friction from the rotor. We have not experienced such failures in our processes, but I have no doubt that it can happen with certain products.
The larger 0.4 mm gap between rotor and stator let the pump pressure recirculate and squeeze the particulate into the space between rotor and stator.The rising pressure through the pump pushes and deforms the rubber in the stator. The sand trapped against the upstream curves of the rotor rip across the deformed rubber stator as the rotor turns and both are scored.
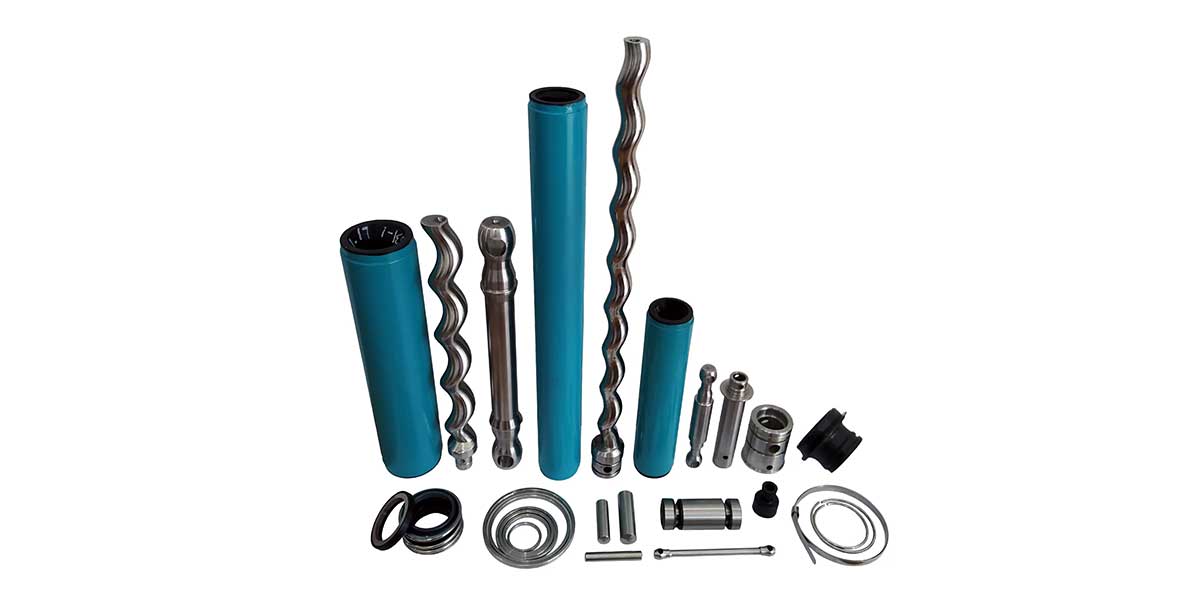

Roller Profiling for Generating the Screw of a Pump with Progressive Cavities
Progressive cavity pumps are used in industry for the circulation of high viscosity fluids, such as crude oil and petroleum products, sewage sludge, oils, salt water, and wastewater. Also known as single screw pumps, these pumps are composed of a single rotor which has the shape of a rounded screw, which moves inside a rubber stator. The stator has an double helical internal surface which, together with the helical surface of the rotor, creates a cavity that moves along the rotor. The movement effect of the cavity inside the stator is the movement of the fluid with a constant flow and high pressure. In this paper, an algorithm for profiling the rollers for generating the helical surface of the pump rotor with progressive cavities is proposed. These rollers are constituted as tools for the plastic deformation of the blank (in case the pump rotor is obtained by volumetric deformation) or for its superficial hardening.To get more news about Screw pump rotor, you can visit hw-screwpump.com official website.
Pumps with progressive cavities allow the circulation of fluids with high viscosity at a constant flow and high pressure [1,2,3]. Among the most used progressive cavity pumps are single screw pumps, consisting of an external helical rotor that rotates eccentrically inside a double internal helical stator [4,5]. The active surface of the rotor is a cylindrical helical surface of constant pitch, and the stator, whose active surface is a double helical surface, is also cylindrical and with constant pitch. The stator is usually made of rubber [6,7], and the rotor is made of steel, often superficially hardened. The exploitation activity of the pumps with progressive cavities has highlighted the fact that traditional pumps with a rubber stator, which surrounds the rotor, do not allow the existence of an interstice between them, which limits their activity until the stator wears out [8,9]. Alternatively, a new class of pumps that do not use elastomers has been developed, in which the rotor and the stator are made of metal, and are used in drilling activities in high temperature wells [10,11,12,13]. This eliminates the wear and greatly increases the lifetime of the pump for use with viscous, high density, and abrasive liquids, and with liquids containing material in suspension. To ensure proper operation, there must be a space between the rotor and the stator to ensure the leakage of the fluid. If this space is not well defined in the rotor and stator design stage, the efficiency of the pump will be seriously affected. Consequently, dimensional designs and optimizations of the rotor and stator, respectively, using analytical and dynamic simulations of the fluid flow through these pumps, have previously been explored [14,15,16,17,18].
The productive functioning of pumps with progressive cavities depends on proper design of the rotor profiles, respecting the technical conditions of their form. The cross-section form of helical pump rotors as ensembles of profiles associated with the rolling centrodes are determined based on the fundamental theorems of the enveloping surfaces (curves) and calculated based on Olivier’s first theorem, the Gohman general theorem, or the Willis theorem (normals method) [19,20].
The geometric characteristics of the rotor, namely, the helical surface with long length and rounded profile, determine that it can be processed by volumetric deformation, using tools in the form of profiled rollers with axes parallel to the axis of the processing blank. The algorithm by which the tool profile can be determined contains the following steps: defining the analytical equations in the own reference system of the piece of the generated profile; defining the absolute movements of the piece and the blank during the generating process; defining the relative movements between the piece and the tool; calculation of the trajectories of the points on the piece profile that execute a relative movement towards the tool; defining the condition which allows the determination of these points, called the enveloping condition—these points belong to the trajectory’s family and to the enveloping of that family; and association of the enveloping condition at the equations of the trajectory’s family, a connection that allows the determination of the parametric equations of the tool profile [21,22]. The tool’s profiling for generating surfaces of the rotors and the stators of the pump can start either from a physical model or from 3D models obtained by rapid prototyping. In practical activity, the determination of the rotor and the stator form can be undertaken with the help of measuring machines in high precision coordinates when the axial profiles of the generating tools in numerical form are known [23]. By comparison, these axial and graphical profiles can be determined using facilities of programming and graphical representation environments, such as the CATIA software application [
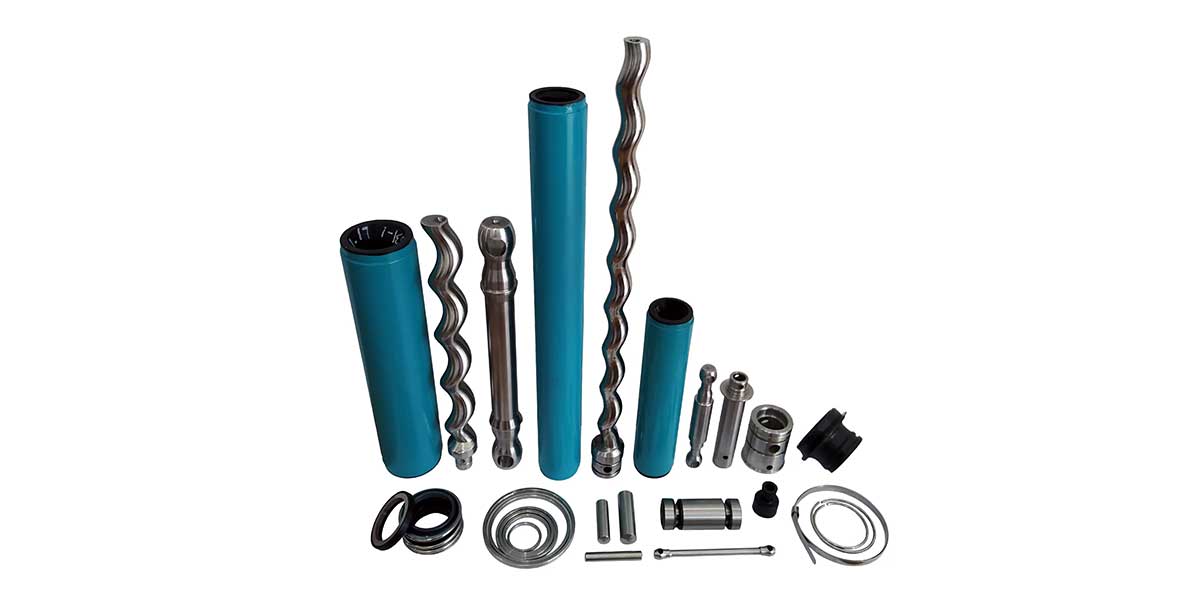

Stators for eccentric screw pumps
In the field of materials handling, progressive cavity pumps are successfully used for tasks that exceed the technical possibilities of pumps of conventional design. They have decisively expanded the range of available conveying systems and are used for conveying highly viscous, abrasive and corrosive media. The components of the progressive cavity pumps are the fixed stator and the rotating component, the rotor. Rotation and the design of both components create chambers through which the respective media are transported from the suction to the discharge side of the pump. To get more news about screw pump stator, you can visit hw-screwpump.com official website.
Stators consist of a steel jacket lined with rubber. The composition of the rubber compound in the stator depends on the requirements of the progressive cavity pumps and the medium to be pumped.
In materials handling technology, not only the abrasion behaviour but also the given physical, chemical and thermal medium properties are important factors that affect the composition of the material in the stator. The rubber mixture is therefore composed in such a way that the material wear of the stator is kept as low as possible. This increases the service life of your stators and prevents costly failures.
In paper mills, pulp, groundwood, glue and paint must be conveyed by means of stators. These are media of crumbly consistency, medium to high viscosity and chemical aggressiveness. The stators from Artemis guarantee a long service life of the progressive cavity pumps.In the food industry, eccentric screw pumps are replacing old, manual processes in the harvesting of grapes, fruit and olives. They are also used in the dairy industry or in the confectionery industry to convey highly pasty masses such as chocolate, marzipan and dough. Our materials and stators used in the food industry meet the strict requirements and quality standards of the food law thanks to our quality controls.
Petroleum industry
Downhole pumps in the field of crude oil production offer a high degree of economic efficiency compared to traditional pumping equipment. Thanks to their easy installation and maintenance, good controllability and high efficiency under difficult pumping conditions, there has been a worldwide increase in the number of pumps. To reduce long downtimes and costs caused by premature failures, we have developed special abrasion-resistant materials for the stators of the downhole pumps. The geometries are fine-tuned to the expected geological temperatures. We offer you complete systems as well as a relining service for worn stators.
Dosing technology
In the electronics industry in particular, ever smaller components must be bonded or encapsulated. One of the main tasks of stators is therefore to convey very small quantities of various media with a high degree of repeat accuracy without dripping. Due to the composition of the materials specifically adapted to the media, our stators achieve the highest possible chemical resistance!
Construction industry
Especially in the construction industry, the screw conveyors have to convey extremely abrasive substances. Artemis offers stators of various designs with a rubber or plastic casing or slotted steel tube for retensioning to prevent wear and tear of the progressive cavity pumps as far as possible. We develop solutions for you so that we achieve an optimum service life for your progressive cavity pump!
Chemical industry
In the chemical industry, the resistance of the stator’s elastomer must meet the highest demands. Media to be pumped can be all kinds of substances, such as filter cake, which has hardly any liquid properties, sludge and many other chemical substances. Our sales teams and laboratory technicians will support you in selecting the appropriate compounds for your application. Our resistance list has proven to be a useful tool in this context.
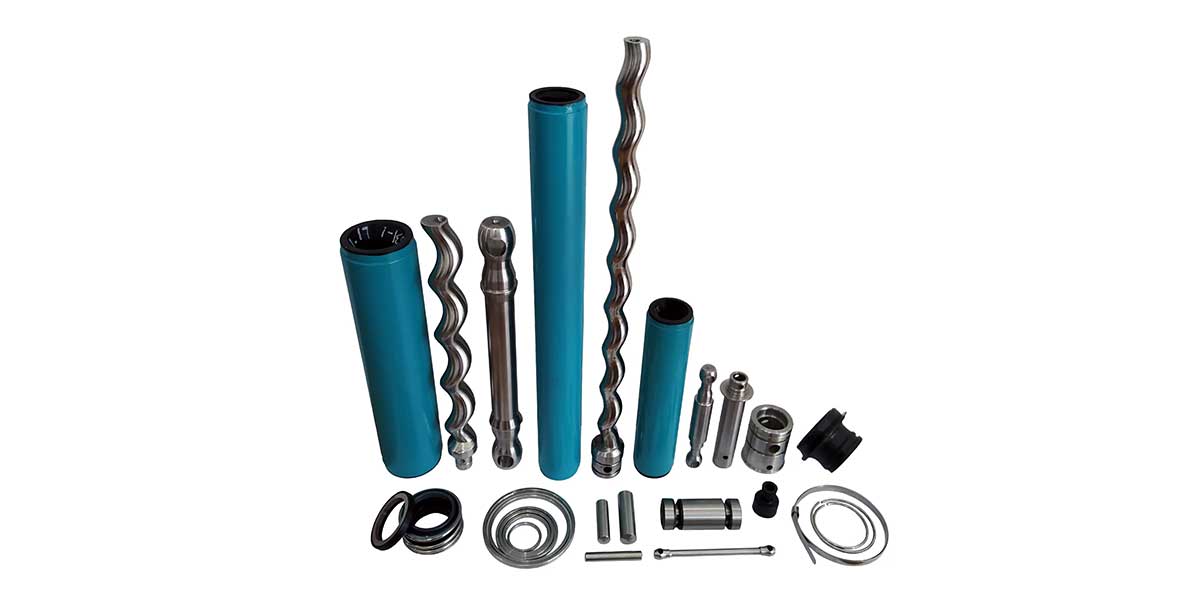