User blogs
Tag Search
Tag search results for: "progressive cavity pump"

PUMPING SOLIDS AND SLUDGES MADE EASY.
Progressive cavity pumps is an extremely versatile positive displacement pump that can be used in a multitude of pumping applications. The best application for a progressive cavity pump is when the liquid contains abrasive solids. Most other types of positive displacement pumps can’t pump solids very well or for very long due to their close tolerances and all metal designs. A progressive cavity pump is designed to last longer than all other pumps on abrasive applications.To get more news about Progressive cavity pump part, you can visit brysonpump.com official website.
These type of pumps transfers fluid by means of the progress, through the pump, of a sequence of small, fixed shape, discrete cavities, as its rotor is turned, which in turn enables nearly pulsation free pumping. The mechanical efficiency and volumetric efficiency goes up when the viscosity increases, lower power and more flow with progressive cavity technology.
Anderson Process is proud to partner with longtime progressive cavity pump manufacturers who are leading the industry in positive displacement progressive cavity pump technology. Our brands include Continental Ultrapump, Flowrox, Flux, Roto Pumps and Standard Pump to offer a large selection of positive displacement progressive cavity pumps for nearly any industrial and sanitary process application.
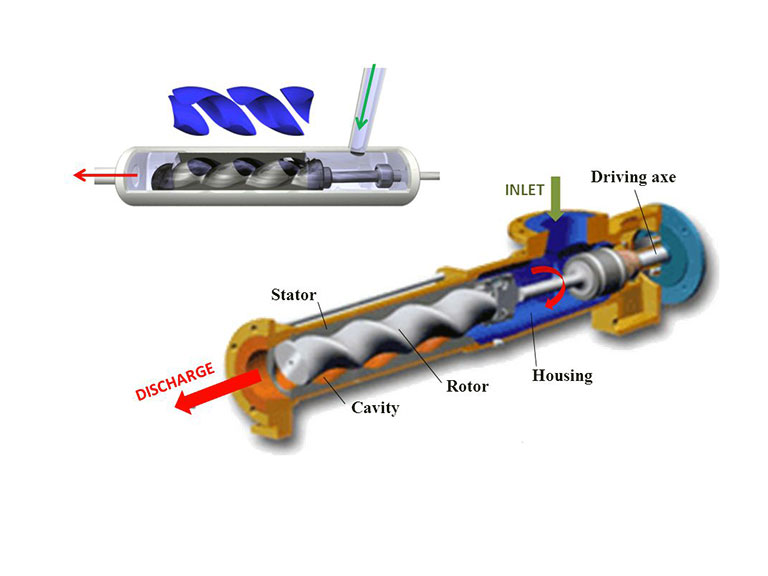

Vote for Best in Show at The ASSEMBLY Show South
More than 150 exhibitors will display the latest manufacturing products and services at the inaugural ASSEMBLY Show South April 4-6 at the Music City Center in Nashville, TN. Fasteners, power tools, adhesives, dispensing equipment, conveyors, robots, software and, of course, automated assembly systems are among the myriad new products on display.To get more news about Progressive Cavity Pump Spare Parts, you can visit brysonpump.com official website.
To draw attention to the breadth and quality of new technologies on display, we’re holding a “Best in Show” contest at the event, and you—the attendees—will be the judges. We’ve nominated 10 products that we think are particularly innovative. All you have to do is vote for your favorite on the show floor.
Modular Platform for Automation
Flexbase is a configurable, modular platform for automation. It enables manufacturers to standardize production equipment, simplify engineering and maintenance, and adapt quickly to rapidly changing production requirements. It also provides a lower risk path to transition manual processes to semiautomatic or fully automatic production.
Available in 4- or 6-foot standard models, Flexbase can be configured as a standalone automated workstation or linked together to create a complete assembly line. Optional conveyors can be configured for over-under pallet recirculation.
The cell is ISO 6 compliant and can be FDA-validated with a documentation package. It has a maximum height of 7.5 feet to fit through a standard 8-foot doorway and includes built-in levelers. It is also ergonomically designed to accommodate a standing or sitting operator. The platform can be used for a variety of processes, including assembly, sorting, testing, handling, fastening and joining.
Fully integrated Allen-Bradley controls are adaptable to various automated operations. The IIoT-ready control system includes IO-link enabled hardware and OEE Optimizer machine analytics software. Booth 329
The Electric EA30 is the first roller-forming machine with servo-controlled articulation. With three individually programmable servos, the Electric EA30 can execute a variety of profile shapes in a single stroke. The forming capabilities include traditional roller forming, articulating roller forming, 3D articulating roller forming, and crimping.
Servo-controlled radial motion delivers higher precision and control compared to conventional equipment, which requires manual adjustment of a mechanical stop. All three servo motors are aligned within the unit, giving the machine a slim design. As a result, the machine is well-suited for integration into automated production lines with limited space. It can also be used as part of a stand-alone work cell for prototyping or low-volume production where frequent changeover of nests and programs may be necessary.
HPPi software allows programming and quick adjustment of the forming process using the HMI. The software monitors all aspects of the forming process and stores the process data. The data can be exported through an industrial data interface (OPC/UA), enabling integration into higher-level production management systems.
The primary advantages of the technology are flexibility in forming; programmability and control of the vertical, radial and rotary motions; and real-time feedback of the forming process parameters. Additionally, this technology can reduce cycle time compared to conventional machines, which may require multiple forming steps to produce the same part. Booth 511
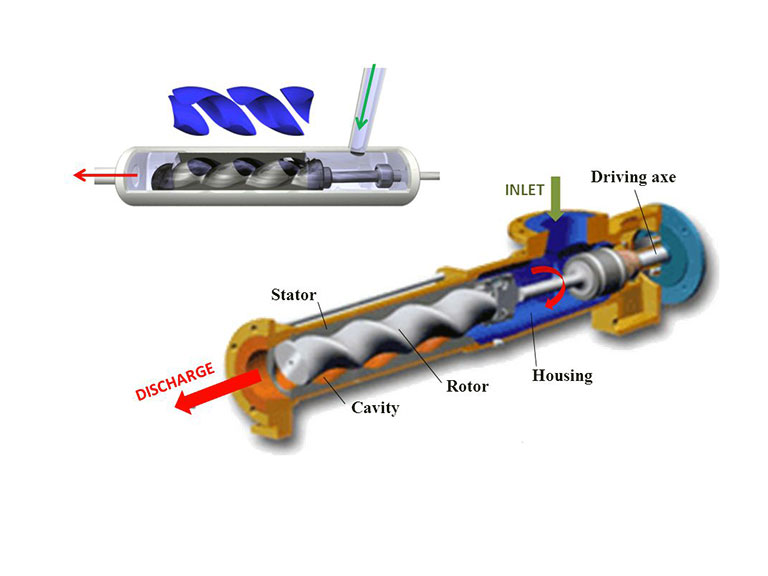

MAKING THE MOST OF PROGRESSING CAVITY PUMPS IN DIFFICULT FOOD AND BEVERAGE APPLICATIONS
While progressing cavity pumps are not the most commonly used option for conveyance in food and beverage production, they are required for certain applications, including those requiring very gentle handling or continuous non-pulsing flow, or for conveying highly viscous media. Progressing cavity pumps can be well-suited to food and beverage applications’ essentials regarding contamination avoidance. With the right system design, progressing cavity pumps can reduce cost, lower maintenance needs, and achieve better results in complex conveying applications within food and beverage production.To get more news about Progressive cavity pump stator, you can visit brysonpump.com official website.
Where food and beverage pumping applications are concerned, progressing cavity pumps are rarely the first thought in system design. Rotary lobe and centrifugal pumps are far more commonly used in these applications, and indeed are often the right choice. In many situations, however, rotary lobe and centrifugal pumps are not up to the task of conveyance in food and beverage applications, or are not the most cost-effective solution.
NETZSCH PumpsProgressing cavity pumps can handle higher pressures and higher viscosity materials than either rotary lobe or centrifugal pumps. Cost savings of up to 50 percent are possible with progressing cavity pumps over rotary lobe pumps, especially in smaller volume operations. The progressive cavity technology can also be designed with an open hopper that allows for the pumping of non-flowing products such as meats and vegetables. The choice in not so clear-cut for applications requiring an extremely small footprint; in these cases, designers must balance the need for the benefits achieved by use of progressing cavity pumps with available space to determine the best solution.
In the end, progressing cavity pumps are ideal for conveyance tasks in a number of food and beverage production environments, especially those with difficult-to-convey, shear-sensitive, abrasive, and/or viscous components. The pumping process in progressing cavity pumps involves a rotor turning with an eccentric rotary motion within a fixed stator. The two components are precisely geometrically mated with one another, conveying chambers are formed between them, and these chambers advance during rotation. The medium is gently transported in these chambers from the inlet to the discharge side by the turning motion. Volume and pressure remain constant with progressing cavity pump technology, regardless of the viscosity or consistency of the substance being conveyed. In addition, no shear forces, pulsation, or pressure reversal points occur, thus avoiding damage to the medium.
In food and beverage applications specifically, progressing cavity pumps must be designed to reduce the risk of contamination and help achieve the targets of the Food and Drug Administration’s (FDA’s) Food Safety Modernization Act (FSMA). To do so, pumps must use FDA- compliant materials, including metals, plastics, and elastomers, with each elastomer compound independently tested to determine suitability and be of a high hygienic design. Depending on the process and the industry, 3-A Sanitary Standards Inc. (3-A SSI) or European Hygienic Engineering and Design Group (EHEDG) certification may be required for pump systems and processes in food and beverage applications.
Making CIP work in PC/PD pumps
NETZSCH PumpsCIP procedures are critically important in food and beverage conveying applications because proper pump and pipe cleaning is key to avoiding contamination, bacterial growth, and other issues. By running a cleaning agent (acids and caustics) through the pump system, proper cleaning can be ensured and regulatory requirements met. It is important therefore to utilize the cleanest possible design within the pump to minimize cleaning time and maximize production time. A well designed CIP system can even be used to CIP open hopper pumps after pumping non flowing products.
Benefits of well-designed pumping technology
It is important to take cleaning into account when first designing the pumping system. The progressing cavity pump rotor should be designed to be compatible with both the process’s media and temperature range and the chemicals being used in the CIP process and their temperature. CIP processes can change, and when they do, compatibility with the stator elastomer should be verified and the stator or cleaning solution replaced if necessary.
Because a separate dedicated pump is used for CIP (usually a small low-cost centrifugal pump), progressing cavity pump design should include the appropriate bypass setup, to ensure that turbulent flow is achieved in both the pump and the piping downstream of the pump. The NETZSCH NEMO® Progressing Cavity Pump is a good example of this kind of design for sanitary applications. With suction and discharge ports located tangential to the body of the pump, the NEMO pumps achieve complete drainage and proper circulation through the pump for cleaning. In addition, NEMO pumps feature open hygienic joints to enable the best cleaning of the joint and the elimination of dead zones that can lead to contamination. NETZSCH with their NEMO Sanitary Plus design also offers flexible connecting rods in lieu of joints, negating any crevices and reducing CIP time even further.
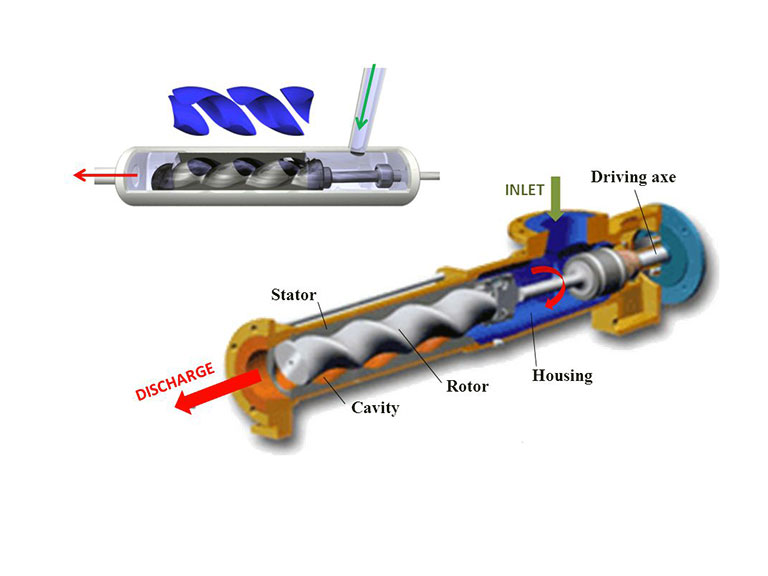

NEMO Multiphase Progressing Cavity Pump
In the past, many oil fields were no longer considered profitable due to unpredictable flow rates. Using multiphase pumps, oil and gas production remains profitable even when the water or sand content in the medium increases. Thanks to the pumping principle, neither space-intensive separation devices at the well nor separate pumps, compressors and lines are necessary to transport gas and liquid to the central collection stations. Multiphase pumps allow you to pump without initial phase separation. In addition, by using the pumps, you conserve natural resources and thus the environment. To get more news about Progressive cavity pump parts, you can visit brysonpump.com official website.
Due to the closed system and the few existing leakage points, flaring in fields is prevented. The highest standards for equipment and safety are an essential requirement for working in oil fields to keep processes safe and reliable. NEMO® pumps contribute to this safety and reliability. The complexity of the pumped media ranges from high viscosity to low viscosity, from shear sensitive to heavily loaded with solids. The innovative and reliable design allows for efficient process control. These multiphase pumps meet the requirements of API 676 3rd Edition and also those of NACE MR-0-175. Safe and reliable pumping with maximum efficiency, NEMO® Multiphase progressing cavity pumps make it possible.
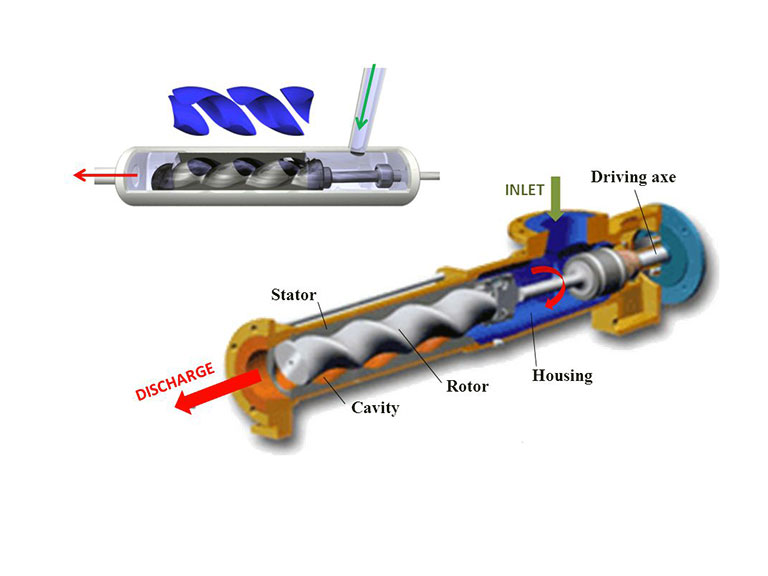

Who Manufactures Progressive Cavity Pumps?
The Dura Pump team is often approached with one frequently-asked question: what manufactures are there of progressive cavity pumps? In our latest blog, we set out the main manufacturers of progressive cavity pumps for the UK market. Read the full piece below and don’t forget to visit our blog for more pump industry insights!To get more news about Progressive cavity pump part, you can visit brysonpump.com official website.
Mono is one of the leading and most well-known brands. This is to the extent that progressive cavity pumps are often referred to as Mono pumps!
The manufacturer of Mono pumps and parts is Novo. This company manufactures a wide product range suitable for the pumping of fluids within the wastewater, chemical, food, beverage, paper, mining, mineral processing, marine, agricultural and oil & gas sectors.
Mono pumps was founded in 1935 in London, UK and has since expanded its manufacturing and operations internationally. They were also the original producers of the EZstrip range of progressive cavity pumps – a real household name.Seepex are another well-known progressive cavity pump manufacturer with their memorable strapline: ‘all things flow’.
They have a large range of progressive cavity pumps for the food and beverage industry, environmental engineering, oil & gas and pharmaceuticals as well as many manufacturing applications. Seepex was founded in 1972 and has continued to expand globally ever since.
Netzsch pumps are a versatile, innovative, high-performance brand providing a wide range of progressive cavity pumps, under the NEMO range, including many specialist solutions to the environmental and energy, food and pharmaceutical, oil and gas, chemicals and mining. Netzsch progressing cavity pumps offer you continuous, pressure-stable, gentle and low-pulsation pumping of a wide variety of media.
Roto Pumps have been manufacturing progressive cavity pumps for more than 50 years and are ranked among one of the top 10 companies in manufacturing positive displacement pumps. With a state of art manufacturing facility, they are continuing to increase their product portfolio covering a wide range of applications, such as chemical, defence, wastewater treatment and agriculture industry.
Sulzer is a global leader in fluid handling engineering, with over 150 years of experience building and developing products and services to drive a more sustainable world. Sulzer operates in some of the largest industries in the world, such as recycling, construction and civils, mining and metals and the power generation industry.
The Sulzer brand was founded, by the Sulzer brothers, in 1834 and its headquarters are currently based in Winterthur, Switzerland. Sulzer offers a wide range of progressive cavity pumps, capable of providing near constant flow rate and suction lift for handling wastewater sludge, slurries, viscous and shear thinning non-Newtonian fluids.
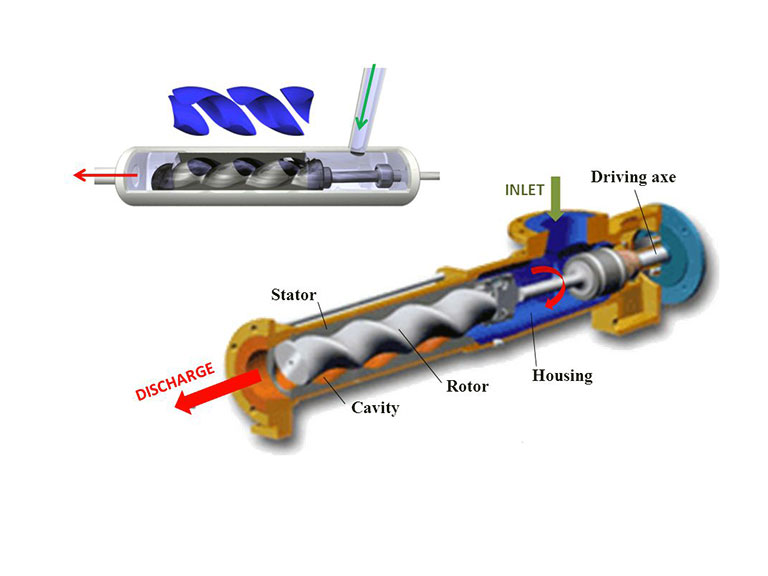

Progressive cavity pump Market
A progressive cavity pump is a type of positive displacement pump and is also known as progg cavity pump, eccentric screw pump or cavity pump. Progressive cavity pump transfers fluid by means of the progress, through the pump of a sequence of small, fixed shape, discrete cavities, at its rotor is turned which leads to the volumetric flow rate being proportional to the pumped fluid. These pumps have application in fluid metering and pumping of vicious or shear sensitive materials. The cavities taper down towards their end and overlap. To get more news about Progressive cavity pump parts, you can visit brysonpump.com official website.
COVID-19 Impact analysis
With the outbreak of COVID-19, the market has witnessed a slump in demand from various enterprises operating in the end-user industries. Under such constrained circumstances, these enterprises have seen a vast decline in revenue and profits, leading to a significant cut down of employees and workers, resulting in an overall loss to industrial production activities. However, players, like Seepex Inc., have witnessed an increase in orders for spare parts. The company has also found alternative supply channels, components within their modular, and varied pump offerings. Governments of several countries across the globe have imposed stringent lockdowns to limit the spread of the coronavirus. Movement of individuals and economic activities, related to goods and services, have come to a halt because of lockdowns. Supply could not adjust to the decline in consumption. This resulted in considerable build-up of crude oil in storage. Therefore, midstream activities (consist of transport of crude oil to the refineries) were hampered. Progressing cavity pumps are extensively utilized in pumping stations, which are part of infrastructure of midstream activities. Thus, unprecedented decline in demand has created difficulties for the upstream sector in regions that have unfavorable production economies, which in turn has hampered the whole supply chain of the oil & gas industry.
Top Impacting Factors
The global progressive cavity pump market is growing at a fast pace owing to driving factors such as increasing demand from water and waste-water industry due to its characteristic of handling high viscosity fluid. Moreover, increasing use in power generation due to low cost is likely to drive the demand for progressive cavity pump in the near future. High to moderate maintenance cost is projected to restrain the growth of progressive cavity pump market
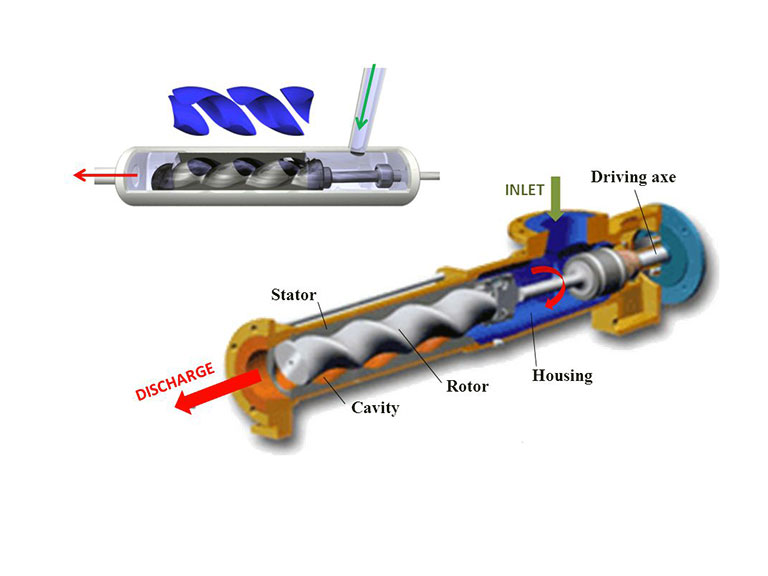